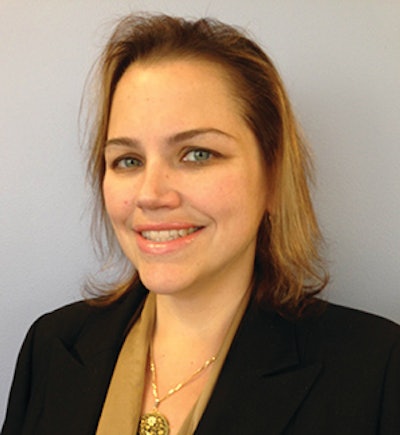
Do you know precisely where any given shipments are currently located? For many shippers and freight forwarders transporting goods around the world, the answer is a resounding “no.” In fact, a recent KPMG study[1] shows that less than one out of 10 shipping professionals has complete visibility into their supply chain, hindering their access to the data clients demand.
It’s an information gap that has proven costly for companies engaged in global trade or logistics management. As organizations work to keep leaner inventories, it’s more important than ever for businesses transporting goods across long distances to stay on top of expected delivery dates and to proactively manage processing delays. For example, retailers facing increasingly slim margins can’t afford to advertise a sale on a popular item if it isn’t on store shelves when expected. Manufacturers must safeguard against ramping manufacturing if a critical part is delayed. In order to drive decisions effectively, businesses need access to complete, timely and accurate information throughout the entire supply chain shipment process.
Fast, reliable access to high-quality data enables businesses to make course corrections and adjustments that protect profits and ensure prompt deliveries. Simply put, if a shipper can’t get the goods delivered on time, their clients and customers can quickly move on to someone who can.
Unfortunately, information transparency in the global ocean shipping industry remains a real challenge. The level of service provided by companies like FedEx and UPS has raised expectations of all logistics providers and their customers since they have been able to supply precise details on every package as it travels to its destination. Through a complete end-to-end system, these companies have comprehensive data from the point of pickup to the point of delivery, giving them a distinct advantage since they control the delivery and information chain. For shippers and freight forwarders who work with multiple carriers around the globe—and are reliant on many service and information partners—the issue of data transparency is a real challenge.
Many of the largest shippers have enough business to dictate a solution. Through the threat of decreased volume, they can mandate that carriers provide solutions for delivering timely, accurate and complete data. Facing loss and negotiated business penalties, many carriers are driven to supplement the systematic delivery of data with manual entry to fill in missing container status events. But what about the rest of the industry? Is it possible for even a small to mid-sized shipper to work with carriers to achieve FedEx-like transparency? Without a systematic approach to data quality improvements, it isn’t feasible for carriers to deliver it.
However, there is a way to achieve data equality for all, regardless of shipper size or regional location. Though there is no single magic bullet, there are three important steps you can take today to shake up the status quo and begin bridging the information gap.
Step 1: Broaden Your Carrier Selection Criteria
A recent survey has revealed that 36 percent of the data received from carriers is considered very poor to average[2]. Even if your firm isn’t large enough to mandate that carriers track and provide the accurate information you need, you do have power—the power of choice. As the need for information increases, companies may find that basing carrier selection on the freight rate alone is not in the best interests of their company and clients, especially when considering the internal costs and time required to fill information gaps. Explore your options and ask questions. Look for carriers who can provide complete, accurate and consistent data—from end to end.
Also, you should look for companies committed to data timeliness. Can your carrier promptly tell you when a ship leaves port or arrives at its destination? Would you know right away whether your cargo has been unloaded or whether there have been delays on the receiving end? If critical information arrives after the fact, you may be in the unfortunate position of saying “I don’t know” when a client asks about status. Or worse yet, you may be forced to deliver bad news when it is already too late in the process for your client to get ahead of issues and solve delays before they impact desired business outcomes. Choose carriers who use technology to systematically improve quality and consistently deliver same-day updates.
Step 2: Adopt an Electronic Shipping Platform
The data you collect from carriers can’t be put to work unless you can use it to benefit your business and customers. You need to be able to absorb and analyze information efficiently—from bill of lading, through tracking and tracing, to final invoice.
Unfortunately, many in the shipping industry are mired in time-consuming, inefficient and error-prone manual processes. Information remains locked in data silos where it is impossible to access it easily—impeding the ability to provide supply chain visibility.
If you want to grow your business, it’s time to adopt an electronic shipping platform that allows you to analyze and act on incoming data faster. With the right software, you can track the progress of each shipment against major milestones, keep your clients informed and take corrective action to prevent impactful delays. You can establish performance metrics for various carriers and lines of business, monitor the results and use what you learn. Plus, carrier performance can be better gauged, leading to more effective strategic sourcing decisions, and the ability to negotiate better terms and rates.
Step 3: Join a Collaborative Network
One final but important step in bridging the information gap is to join a collaborative industry network. When you do, you have a window into real-time container status and operational data from all participating carriers and transportation sources—accessible over a shared, online platform. All participants draw from the same information and have a mechanism to collaborate on solutions in real time.
According to a recent analyst report, “Only the power of a shared, collaborative platform connecting multiple business partners of the supply chain network can drive high data transparency.[3]” Collaborative networks are the wave of the future and offer the best way to achieve a high level of visibility across the entire supply chain. The larger the network, the broader your access to the right information.
A collaborative network can also resolve standards issues. For example, to date there has been little industry consensus on the definitions of the critical points in the shipping chain when data should be captured and recorded. Has a container arrived when a ship enters port? When it is unloaded at the dock? When the contents have been turned over to ground transport? A collaborative network is positioned to broker a consensus on such definitions and to mandate a consistent, standards-based approach.
Stake a Claim for Data Equality
It’s clear that that access to data shouldn’t be reserved only for the largest companies. Shippers should select carriers who are able to provide complete, accurate and consistent data to shippers of all sizes—in time to proactively respond. Moreover, if manual processes continue to plague your ability to conduct business with accuracy and speed, it’s time to adopt electronic shipping processes and enabling technologies. Joining with a network of your industry peers who are committed to informational transparency—and data equality for all—can enable you to track, trace and manage your supply chain in proactive and predictive ways, which in turn, helps you exceed customer expectations and ultimately boosts your bottom line.
[1] KPMG Global Manufacturing Outlook: Competitive Advantage. 2013
[2] Source: American Shipper’s ITM Benchmark Study
[3] Gartner Report: Multiple Processes, Partners and Data Objects Must Be Considered to Obtain Benefits From Supply Chain Visibility --July 25, 2013 G00250647. By Christian Titze, William McNeil, Ray Barger, Jr.