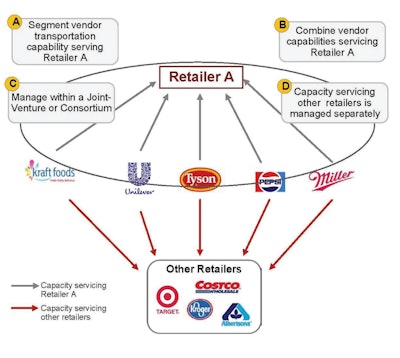
The U.S. economy and freight industry are growing again. Overall revenues increased eight percent in 2010, after falling 25 percent in 2009. And while most U.S. organizations are struggling to close the gap between their desired and achieved levels of transportation performance (see figure 2), they don’t consider certain performance metrics—such as carbon footprint—as key to their overall success.
What is quickly becoming clear to shippers and carriers is that the U.S. freight industry is fast approaching its “used-by-date” plateau in its ability to further lower cost-to-serve. This industry is converging towards its new equilibrium which promises to be a combination of two models—cross-firm collaboration and modal optimization with an emphasis on sustainability. The new equilibrium promises a $6 billion to $15 billion opportunity in the U.S. alone. And the speed of migration will depend on how rapidly the “first movers,” i.e., the shipper industry titans, gather momentum and provide scale to the new equilibrium. These and other findings are among the main results of an A.T. Kearney study of the U.S. freight industry.
Based on a survey of 154 decision-makers across consumer products, food & beverage (F&B) and chemicals manufacturing industries, AMR Research highlighted three primary challenges, amongst several others, which the industry and its participants face: deadhead miles and asset utilization; cost to serve; and sustainability.
Deadhead miles and asset utilization
Suppliers, manufacturers, retailers and transportation providers are all looking for ways to further reduce costs but can only make relatively small improvements. In 2010, the U.S. freight industry was estimated to be $655 billion, $523 billion of which was in commercial and private truck loads, according to American Trucking Associations’ “U.S. Freight Transportation Forecast to 2023” report. Deadhead miles accounted for about 10 percent of the mileage for the five major U.S. truck-load carriers, and even higher for private and dedicated fleets over the past five years (see figure 3). Our conservative estimates lead us to believe that completely reducing deadhead miles for commercial and private truck load moves could eliminate at least 64 billion miles of traffic or yield almost $60 billion in incremental revenues for the industry—if the empty mile cost can be captured in service. Part of the reason for these inefficiencies is structural (nature of transportation flows) and part of it is asymmetric information (lack of visibility to combined transportation networks). Which factor contributes to what degree of inefficiency is unknown. A.T. Kearney’s survey of large shippers suggests 10 to 25 percent of this opportunity ($6 billion to $15 billion) can be captured depending on the future operating model of the U.S. freight industry.
Cost to serve
Each transportation mode has unique challenges in maintaining the same service levels with fewer resources. Truckload suffers from strict regulations such as hours of service; insurance costs; rising fuel prices; and scarcity of capital to purchase new equipment. Intermodal is more economical than trucking but suffers from delays, product damage and limited network coverage. Air, which benefits from faster and more accurate delivery times, faces high fuel and equipment costs. Less than truckload (LTL), which offers cost advantage relative to air for overnight/second day deliveries, suffers from high overhead and handling costs.
Sustainability
The fact that the transportation sector contributes more than five percent (2,800 tons) of all carbon emissions in the U.S. is not lost on freight industry participants. More than 86 percent of the 150 companies polled have tried to (or plan to) improve their sustainability initiatives. Their options, however, vary in impact and effort required. Some involve the replacement of transportation vehicles while others involve the indirect efforts to reduce congestion.
The U.S. freight industry’s transportation broker market is analogous to a trading floor on which transportation lanes are traded among freight carriers and shippers. Major players—such as C.H. Robinson Worldwide Inc. and Coyote Logistics LLC—have value propositions which include: real-time visibility to transportation capacity by lane/mode across several carriers and independent owners; access to several shippers’ supply chain networks and the customized requirements; established relationships that match demand and supply for transportation to minimize total cost-to-serve; and expertise and state-of-the-art tools to optimize carriers’ and shippers’ supply chains.
Emerging trends—collaboration and modal optimization
While the transportation broker market helped cut deadhead miles in the freight industry, there are still substantial opportunities for U.S. carriers and private fleets to reduce them even more. And reducing deadhead miles has become a multi-billion dollar opportunity that spawned two new trends: collaboration and modal optimization.
Generally speaking, collaboration refers to developing partnerships among players all along the value chain—both vertically and horizontally. Modal optimization refers to cutting costs and improving efficiency. Total transportation costs fall by building larger and more economical loads across modes or shifting to more economical modes.
These trends not only helped companies reduce their deadhead miles but also their costs for overall transportation and other supply chain activities such as storage and handling. And they helped create sustainable solutions by enabling more efficient use of transportation assets.
In addition, there is an opportunity to use collaboration (vertical and horizontal) and modal optimization to improve asset utilization and reduce supply chain costs by up to 30 percent.
Vertical collaboration refers to partnerships among players across the value chain, for example, consumer products companies (CPGs) with their raw material suppliers and retailers. The benefits of vertical collaboration include complementary transportation networks, scale and best-practice sharing. To date, the electronics and auto industries have successfully implemented this type of collaboration. Third-party logistics (3PL) provider Verst Group Logistics uses collaborative distribution to transport automotive parts from as many as 15 parts makers to Toyota, General Motors and Chrysler—a process which yielded a 30 percent reduction in supply chain costs.
Horizontal collaboration involves partnerships among players within the same layer of the value chain, for example, two CPGs or two retailers. The benefits include scale, improved product mix and similar origin and destination pairs. CPGs have successfully implemented horizontal collaboration in both the U.S. and Europe. DeMet's Candy Co., The Topps Co. Inc. and Sun-Maid Growers use a collaborative Kane-run distribution center. 3PL Kane Is Able gives cash rebates to retailers that participate in collaborative distribution. Retailers coordinate orders and manage delivery schedules.
At the same time that freight companies are starting to collaborate, they are also focusing on modal optimization to lower cost-to-serve and improve customer service levels. Increasing fuel prices and technological advancements in the transportation equipment and infrastructure industries have accentuated this trend.
This shift from single-modal to multi-modal shipments also blurred the lines between mode definitions. For instance, LTL increasingly encroaches on air space for next-day deliveries. Similarly, the greater-than-800 mile threshold no longer holds true for the “intermodal over TL” decision, with line-hauls as short as 600 miles shipped intermodal. DHL rolled out multimodal services from China to overseas markets including the U.S. in July 2010. As part of its goal to reduce cost-to-serve, the company combines air, over-the-road (OTR), rail and ocean into complex multi-stop (yet cheaper) routes for moving cargo from China to the rest of world. It expects to cut its transportation costs 20 to 50 percent by reducing deadhead miles, cost of handling and cost of storage.
Modal optimization using multi-modal shipments is gaining momentum because of the increasing pressure to lower costs of transportation. The Dial Corporation (a Henkel company) reported 35 percent cost savings since relying on multi-modal transportation for years now. Dial worked with its suppliers to have chemicals shipped in ISO tank containers by double-stack trains. These containers are drayed to a truck at the destination terminal to be shipped to Dial’s plant, resulting in lower waste and transportation costs. Similarly, pulp and paper industry supplier Eka Chemicals (of AkzoNobel) lowered its transportation costs by shipping products by rail to trans-load facilities and then delivering them to customers by LTL.
Operating models of the future
An operating model based on collaboration and modal optimization will best address the industry challenges. Major benefits of the multimodal approach include improved equipment utilization; reduction of deadhead miles; reduction in lane rates; lower capacity challenges; reduced total transportation/logistics costs; and reduction in greenhouse gas emissions.
Within vertical collaboration, two operating models are vying for advantage: retail-centric and integrated transportation. One or both are likely to emerge as viable in the near future as businesses in the transportation industry begin to engage in large-scale vertical collaboration.
Likely to emerge first, the retail-centric model will entail the retail giants to form exclusive alliances with their suppliers. With such a model, a retailer will manage its own transportation network and the part of its suppliers’ transportation networks used to serve that particular retailer through a joint venture or consortium with suppliers (see figure 9). This retail-centric collaboration will cause the retailer’s network to become fully optimized, reducing deadhead miles and increasing asset utilization. These actions will also reduce the carrier’s cost to serve and result in more sustainable solutions. Retailers adopting such models will share part of the cost-to-serve efficiencies with their participating suppliers. However, the suppliers’ remaining networks—which might be utilized to serve other retailers—are likely to become de-optimized due to a lack of scale, forcing other retailers to form their own similar joint venture or consortium to avoid becoming marginalized by their competitors.
An integrated transportation model will eventually be the more optimal solution since it will look at all retailers’ and suppliers’ networks in totality. Here, retailers and suppliers form a jointly-owned transportation management business unit that manages the combined transportation networks of all participating retailers and suppliers collectively, as a 3PL would do (see figure 10). The value captured by collectively managing all participants’ networks will be shared based on a variety of metrics including scale and stake in the transportation management business unit. This model will provide the maximum value capture because the transportation networks of a number of retailers and suppliers will be optimized together as opposed to optimizing individual retailers’ networks. This joint optimization will lead to even greater asset utilization and further lowering of cost to serve as compared to the retail-centric model. However, it will require competing retailers and suppliers to develop the level of trust needed to be able to work together. Both vertical collaboration models will help retailers and suppliers capture benefits they would otherwise be unable to capture by continuing to operate as independent entities. However, as figure 11 shows, the integrated model goes a few steps further than the retail-centric model by exercising additional benefit levers and expanding the realm of benefits.
External service provider
Horizontal collaboration, which can be implemented in parallel with vertical collaboration, can yield incremental value. One operating model is to appoint an external service provider, i.e., a multi-client 4PL. This is a quick and easy strategy for starting the collaboration process. It entails extending the typical 3PL role—which is to serve each client individually—to serving all clients involved in a collaboration process as one large client. This option has few integration requirements since the 3PL provides an integrated service for all participants. On the downside, however, 3PLs charge commissions, do not always provide full transparency and sometimes take more than their fair share of value capture—all of which reduces the total value created for the participants. Nonetheless, it is a good option for getting the collaboration process started.
Joint venture
This option provides higher value capture than can be achieved by appointing a multi-client 4PL but it demands a higher level of integration among the transportation functions of the participating entities. Eliminating an external 3PL service provider leaves higher savings to be shared among the participating entities. However, doing so requires several enablers including data transparency; coordination of bidding cycles; standardization of systems; and above all, a certain level of trust. Compared to a 4PL, this option is a more evolved state of collaboration that has its inherent advantages but may take time to mature.
Benefits reconfirmed
The operating model discussed in this paper is sustainable for two reasons: there is a monetary component and an opportunity for all concerned parties—shippers, carriers and 3PL providers—to benefit. What is required, however, is the trust and willingness to work together, especially on behalf of shippers. Look for part two of our series in September, which will cover the seven best practices for multi-modal operation.