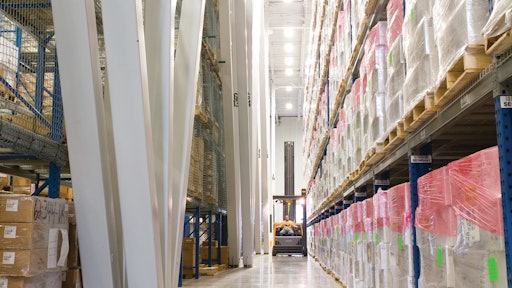
As a provider of dental and medical imaging systems and healthcare IT solutions, Rochester, N.Y.-based Carestream Health Inc. knows that when it comes to patient care, a delayed diagnosis or postponement of treatment due to equipment downtime is not an option. The company’s products and solutions—from medical printing and mammographic imaging products to dental x-ray units and filters—are critical tools to help practitioners be more efficient and productive, and help deliver better patient care. And its highly-trained field engineers stand ready to service the tens of thousands of products installed in thousands of medical offices across the globe. This includes the delivery and installation of parts either the same day or next business day after a service order is placed. And this commitment to customer service and patient care makes it imperative that its field engineers have rapid access to those critical parts once an order is placed.
But the ongoing challenge to maintain the high service levels their customers expect while also controlling costs associated with these services remains.
Carestream Health realized that it needed to improve its manual processes to help reduce costs. The company quickly learned that it would also gain efficiencies by having better control of parts allocation in the field, which would reduce the number of repeat technician visits. That’s when they turned to UPS for assistance to re-engineer the field parts planning and replenishment process. With thousands of parts in the network, the potential for improved efficiency was substantial.
Integrated parts development
The first step was to store Carestream Health’s service parts in 70 convenient UPS field stocking locations (FSL) around the world, which reduced the critical spares inventory and improved customer service since the FSLs are fully integrated into UPS’s global transportation network, ensuring easy access and reliable same-day service to customers.
Next, Carestream Health—along with UPS and its partner Baxter Planning Systems—established a fully integrated parts planning and service parts logistics solution to the field engineer inventory locations, also known as “trunk stock.” Using planning software, a team of UPS and Baxter consultants analyzed everything—from the inventory that each field engineer held in their trunk stock, to the optimal time to reorder parts, to the specific location of where those parts should be stored. This detailed analysis gave Carestream Health confidence that the UPS solution would be successful, ensuring that the right part is available at the right place at the right time, while minimizing inventory.
A pilot was conducted with a group of field engineers using the new planning software to manage their inventory and FSLs. At the end of the pilot, Carestream Health found that priority orders placed by the field engineers were reduced by an average of 23 percent; the field engineers’ inventory dollars were reduced by 12 percent; and the engineers’ first-call completion rate was increased by three percent for all calls. Based on the results from the pilot, the projected saving from this program is more than $500,000 per year.
As a result, Carestream Health now sees the benefits of using the field planning program with reduced number of priority order shipments and reduction in field inventory while at the same time being able to continue the same high level of service their customers expect.
Today, the medical imaging provider’s employees and field engineers have full visibility and quick access to its entire critical parts inventory. Field engineer inventory is aligned with their customer requirements. Through the UPS Order Management System, Carestream Health is able to place orders at the nearest FSL, determine the fastest and most efficient route to the destination and track the shipment every step of the way. In addition, emergency field engineer orders have been reduced. The remaining orders are delivered within a few hours, or in other cases, the field engineer will pick up a part directly from a nearby FSL to save transportation expenses. The system also optimizes the replenishment of parts, including what parts to ship, what field engineer or FSL it should go to and when.
“Using UPS’s FSL network and field planning from Baxter Planning will give Carestream Health’s field engineers a competitive edge in the service and support marketplace. We expect the improvements to grow as we continue to use these tools,” said Randal Hill, Service Parts Operation Manager for Carestream Health.
With operations in 150 countries, Carestream Health knows that when it’s ready to incorporate the system management tool into its global operations, UPS’s network of over 900 field stocking locations, along with its global IT platform, is available to assist in its efforts.