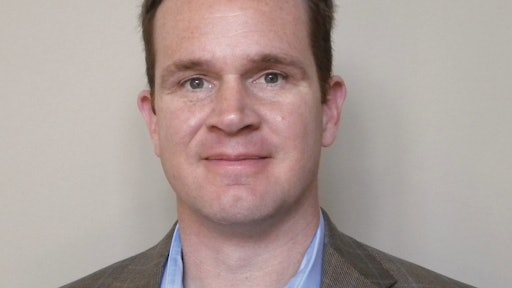
Sales and operations planning (S&OP) is similar to investing in gold: it gets a lot of attention during tough economic times. Sure enough, the economic downturn over the past two years has seen a steady resurgence of companies pursuing S&OP initiatives. Companies running S&OP improvement initiatives are aiming to achieve the overarching benefits of improved service levels and lower supply chain costs. Extensive research has shown companies running best-in-class S&OP do indeed have supply chain cost advantages over their competition. However, is the current S&OP business process the best that supply chain planning can achieve? Or are there methods to enhance the process?
The depressed world economy not only has led to increased activity in S&OP but also forced companies to scrutinize their working capital investments. As a result, inventory optimization became a popular initiative as companies race to right-size their working capital investment. Inventory optimization excels at this goal by utilizing software algorithms to plan to service level targets instead of leaving the planner to rely on rules-of-thumb. However, inventory optimization has mainly been implemented as an adjunct process to Materials Requirements Planning (MRP) and Dividend Reinvestment Planning (DRP) focused on the short-term planning cycle, and not linked to a company's S&OP process.
Both S&OP and inventory optimization use much of the same data and involve most of the same corporate stakeholders. It is the marriage of S&OP and inventory optimization that can create an even more powerful planning process. With the additional capabilities to plan service levels and truly optimize inventory investment, sales, inventory & operations planning (SI&OP) is the next evolution in supply chain planning. This article discusses how companies seeking a competitive advantage in supply chain can integrate inventory optimization into S&OP to create an advanced SI&OP process.
Back to S&OP basics
Sales and operations planning steadily moved higher on corporate agendas as more executives realized the power of aligning demand and supply. Companies are pursuing S&OP for its high-impact benefits. The benefits of a well-executed process include reduced inventory, reduced expedited transportation costs, increased forecast accuracy, improved service levels and quicker decision-making. A 2010 Aberdeen Group survey corroborates this linkage by indicating the top two reasons companies were pursuing S&OP improvements: 1) to improve top line sales revenue and 2) to reduce supply chain operating costs.
Since the earliest days when the term S&OP was first coined, its process witnessed consistent improvement. Evolutionary improvements include both the integration of finance and the emphasis on new product launches. The classic model starts with demand planning followed by supply planning. It is in these first two steps that most of the work occurs. The outputs are a constrained supply plan and usually a number of supply issues. Steps three and four are meetings to review the exceptions, align stakeholders and resolve the outstanding issues. Since the classic model serves as a guideline, it does allow for a wide variety of sophistication in the demand planning and supply planning steps. Two separate companies could be doing both steps but at vastly different levels of detail and proficiency. For instance, some companies have not fully embraced the use of statistical software or even the measurement of forecast accuracy in demand planning.
However, it is in supply planning where the most common deficiency resides. Many companies neglect to take service-level targets into account during supply planning. Instead, many inventory planning processes include a calculation for safety stock or even a simple rule-of-thumb (for example, four weeks of safety stock). While these approaches are most common, they are not best-in-class. The ability to calculate inventory levels based on service-level goals allows for optimal levels of inventory investment.
A company operating on the lower end of the maturity scale for both demand and supply planning would find itself at a disadvantage in S&OP. The company would simply be manufacturing to past history in demand planning and would face overblown inventory targets in supply planning. A company in this situation would have inherent waste in its supply chain from buffering against uncertainty. Such a company can improve its demand-planning woes by employing statistical forecasting software and measuring forecast accuracy.
However, improving supply planning to reduce uncertainty is more difficult. Introducing the dynamic calculation of inventory targets optimized for service-level goals is not functionality included in ERP packages. Yet, the complementary business process and software of inventory optimization do address this gap in supply planning. Introducing inventory optimization into supply planning is an opportunity to enhance S&OP. Considering very few companies today use S&OP and inventory optimization together, it is an opportunity waiting to be exploited.
Calculate in inventory optimization
Inventory optimization is a fast-growing capability as companies have focused on working capital reduction in the wake of the economic downturn. It is itself an evolution of inventory target setting. In the past, inventory targets were typically set by a derived static formula such as weeks of supply. Many ERP systems have fields for inventory parameters that are user-defined fields. In other words, the ERP system is relying on the users to specify the safety stock, reorder points, and minimums and maximums.
Inventory optimization is an advancement of this practice because it utilizes software algorithms to plan a service-level goal for each SKU. The software takes into account the service-level goals, demand volatility and lead-time variability for each specific SKU to optimize the inventory levels. The result is an enhanced inventory planning process that reduces excess inventory and improves the service-level performance for SKUs with stock-out occurrences. This scientific approach to inventory planning has produced significant benefits. Companies often claim a 15 to 30 percent reduction in inventory with a ten to 25 percent increase in service level within the first year.
While inventory optimization and S&OP use the same demand plan, inventory optimization has typically been implemented as a standalone process. In fact, many inventory optimization software packages have built-in demand planning capability. This functional duplication with S&OP further attests to the practical exclusivity of the two processes. Companies tend to implement inventory optimization for use with MRP or DRP and focus its use on the short-term time horizon. So while inventory optimization has driven results for the companies employing it, the process has not been typically integrated into a company's overall S&OP process.
The power of SI&OP
As we discussed above, a common gap in S&OP centers on service-level planning. What if the service-level planning from inventory optimization could be spliced into the S&OP process? The result would be a more robust process to align supply to demand through improved inventory planning. The integration of S&OP and inventory optimization can create a greatly enhanced process known as sales, inventory & operations planning (SI&OP). While SI&OP is most commonly used as a term synonymous with S&OP, its process entails utilizing inventory optimization techniques instead of traditional inventory planning processes.
The power of SI&OP lies in its capability to optimize inventory based on service-level goals. The increased rigor of inventory planning can be applied across the entire S&OP time horizon to drive enhanced supply decisions. Supply decisions can be made to fulfill demand from either finished stocks or further upstream into the production pipeline. Figure 2 depicts the five step process of SI&OP and where inventory optimization integrates.
Get started on your path to SI&OP success
Every company whose goal is to move to an SI&OP process will have a different starting point. The length of the journey and the extent of change depend upon the maturity of the current S&OP process. Companies with robust S&OP will have a quicker path to SI&OP than those companies implementing S&OP for the first time. Regardless of a company's particular starting point, there are three distinct steps that are proven as an effective path to building a SI&OP process.
The first step is to improve the existing S&OP process to best-in-class. Whether starting from scratch or making a few minor tweaks, the establishment of a strong S&OP process is the foundation for SI&OP. The aspects of a best-in-class S&OP are also characteristics that make up a successful SI&OP. Data integrity, managing by exception, financial integration, executive involvement and meeting discipline all serve to create a strong, successful SI&OP platform.
The second step is to install an inventory optimization capability. Getting inventory optimization up and running can be done one of two ways. A company can choose to implement software in-house or use a service provider in an outsourced arrangement. An outsourced provider hosting the software can help get an inventory optimization capability up and running much more quickly than selecting and implementing software in-house. An in-house implementation could take up to a year to go live, while an outsourced provider can have the system up and running in as little as three months.
Once S&OP and inventory optimization are up and running well, it is much easier to integrate the two processes than it would be to implement SI&OP from scratch without a solid S&OP process in place. The final step in the journey to SI&OP is to combine the two processes. Incorporating inventory optimization as Step two requires integration both upstream with demand planning as well as downstream with supply planning. Since forecasting is already an input to inventory optimization, the work to integrate upstream consists of expanding the forecast horizon to equal that used in S&OP.
Now to splice the output of inventory optimization downstream into supply planning, the recommended inventory levels and replenishment orders must feed the supply plan. A key difference between S&OP and SI&OP is the replenishment orders that feed supply planning. The replenishment orders in SI&OP are now calculated from inventory parameters that are optimized based on service-level targets. Supply planning benefits from a more precise derivation of replenishment order to create both production requests for internally manufactured items and purchase orders for purchased items. The more precise replenishment orders allow for overall inventory reduction and increased service levels.
Special care should be given to organizational change. The change in roles and responsibilities must be clearly defined. Of special consideration will be ownership of the final forecast as most inventory optimization software has demand planning capability that is duplicative if the organization already uses a system for forecasting. A rationalization of IT systems will have implications for the forecast ownership. Attention should also be given to align metrics and incentives to drive the desired behavior. Overall, the migration to an SI&OP process is a complicated initiative that requires not only process and system expertise but also focus on the soft issues of people management to ensure a successful launch.
The sum of it all
Like all business practices, S&OP has evolved over the years. While many companies may be following all of the prescribed steps of a best-in-class S&OP process, there may be capabilities not being utilized. Most notably, the optimization of inventory planning based on service-level targets is often overlooked in a traditional S&OP process. The next evolution of S&OP is the integration of inventory optimization capabilities. Inventory optimization provides companies with a scientific approach to dynamically plan inventory to meet desired service levels. It is the inclusion of this service-level planning that makes SI&OP a more effective planning process than traditional S&OP.
A robust S&OP process is the building block upon which to add inventory optimization and create an integrated SI&OP process. The company that extends its capability beyond S&OP to SI&OP will reap the benefits of lowered working capital investment, improved service levels and increased sales.
Mike Valentine is Director, Supply Chain Design & Innovation at UTi Worldwide, Long Beach, Calif., a global logistics provider specializing in inventory optimization services. Reach him at [email protected].