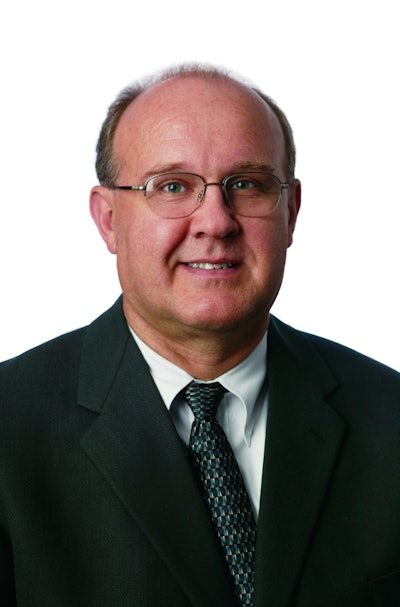
Takeaways:
- Better inventory visibility and forecasting by retailers means fewer rush shipments throughout the supply chain to replenish out-of-stocks.
- It’s critical to plan optimal loads, evaluate modal choices daily, and creatively find capacity in the most efficient manner possible.
- Cost savings from green initiatives improve their bottom line, and green practices are increasingly being scrutinized by customers as an indicator of their value as a business partner.
Most supply chain professionals don’t start their major logistics planning exercises with the question, “How can I minimize the environmental impact of our operations.” But they should, for the simple reason that it makes good business sense.
Today, the best planners are minimizing their company’s carbon footprint and environmental impact by focusing on profitability. By reducing expensive rush shipments, better planning a truck route, or gaining better visibility into the supply chain, they enable “slow, green” shipping decisions – decisions that are green in an environmental as well as a financial sense.
The Bullwhip Effect
Retailers can have the most dramatic green impact throughout the supply chain. They control packaging requirements, favor suppliers with green packaging, and choose products with sustainable ingredients and components. Most importantly, retailers can improve forecasting, dramatically impacting global shipping operations.
Think about the bullwhip effect of forecasting at retail – akin to the metaphor of a butterfly flapping its wings. If a product runs low and a retailer places a rush order for 10 percent more than it needs, there is a natural shockwave throughout the supply chain. The manufacturer decides to add 20 percent to the forecast to be safe, then component manufacturers jump through hoops to build 30 percent more materials for their own buffer.
So the wings flapping at the retail planner’s desk create a tidal wave of unnecessary air freight shipments, ill-advised execution strategies, and short manufacturing runs – all of which tremendously increase the carbon impact throughout the supply chain.
It doesn’t have to be that way. Better inventory visibility and forecasting by retailers mean fewer rush shipments throughout the supply chain to replenish out-of-stocks. With more enhanced awareness of enterprise-wide inventory levels and a flexible approach to fulfilling those orders from other sources, retailers can go green – both environmentally and financially.
That’s why good visibility and analysis software tools are so critical. For instance, they can help identify if too much product is on the West Coast when it will be needed soon on the East Coast. Also, visibility into suppliers’ operations helps retailers to make a more-informed business decision to drop-ship from a supplier to the store or warehouse, or direct to the customer.
Looking at reverse logistics, unsold goods are often pushed back to the DC, a hugely inefficient process. Another option that is often overlooked is to sell those goods from their present location via e-commerce channels, requiring fewer moves.
Retailers should also embrace a demand-based forecast with integrations to POS data to realign the forecast daily and send consistent, clear demand signals upstream to warehouses and suppliers. Better forecasts and more frequent updates to suppliers reduce the bullwhip effect, minimize panic, and thereby allow all parties to make greener decisions.
The Slow Boat…or Truck…or Train
Logistics planners have a different challenge, but one that is just as important to a slow, green approach. They have to consider many modes – boat, rail, truck, fleet vehicles or parcel. That’s why it’s critical to plan optimal loads, evaluate modal choices daily, and creatively find capacity in the most efficient manner possible.
Trains are commonly greener for long-haul shipments, while trucks can be greener for the short haul – which is why it is important to use software tools to crunch the numbers every day and confirm available capacity for those modes. In fact, shipments can travel at greatly reduced rates if they are assigned to a vehicle that is already planned for movement, reducing the carbon impact by not having to create a second trip.
For those companies that own their own fleets, the more freight that is put on each route eliminates the potential need to send additional trucks. TMS solutions can help optimize asset utilization and build safe/legal loads, all without overfilling or crushing goods. This strategic approach helps to reduce the amount of trucks that have to be dispatched.
For instance, logistics managers often see five full loads going south while a half load remains at the DC or warehouse. In a slow, green supply chain, the half load can be held back and matched with tomorrow’s shipments to make more full loads. Another option may be to release more orders for that part of the country and fill the sixth truck today.
Another great negative impact on green trucking is the amount of assets that travel empty on our roads and highways. By embracing Continuous Move concepts, companies can tender a set of deliveries with pickups. They will add capacity to otherwise empty assets, and can also negotiate attractive carrier backhaul rates at the same time.
For a company that has always done shipments over the road, reconsidering ways to leverage rail shipments is another slow, green option. By evaluating rail and piggyback trailers, and then calculating the cost and time compared to over-the-road trailers, companies who have their product ride the rails can be more effective and green.
Ships travel at different speeds, but it’s not always true that the slower ships are more fuel efficient or greener. Super ships can produce fewer emissions per hundredweight on-board. The age of the equipment also is critical to the environmental impact, since older equipment is much less fuel efficient (which applies to all modes of shipping). Some industry organizations are working to offer ways to evaluate these kinds of “green” criteria, so it is easier to evaluate greener equipment and logistics operators – an emerging science that is going to be interesting as it evolves.
Don’t Press the Panic Button
Better planning that incorporates the green factor into the equation can also alleviate partner “panic” levels in the supply chain, which leads to reduced supply chain expenses. A good TMS solution helps long-term planning and evaluation of freight options with the best carbon footprint – slow shipping options that are also less costly. Operators who use best-of-breed TMS systems also feel more in control, and are comfortable keeping inventory buffers and safety stock at desirable low levels while using slow transit.
TMS software assigns the optimal carrier based on when product can be shipped and the available vehicle capacity – all automated in a load-planning function. Business rules also ensure the plan can be met based on constraints of all the parts. For example, the system won’t set up a multi-modal truck-to-rail shipment if the train is scheduled to depart before the truck can arrive. The TMS planning engine takes into account constraints of schedule, pickup and delivery windows, available equipment and capacity, and time latency between dock and delivery – and then uses business rules to select the most cost-effective and efficient modes for every order.
Companies can also consider other green aspects of their operations relative to speed. For example, a second shift helps provide more same-day shipments, but the financial trade-off is the investment in resources such as lights, heat, equipment and power needed to run the second shift. Eliminating the need for a second shift can result in money and energy savings in the long run.
Slow, green supply chain tracking will continue to evolve and ultimately influence consumer behavior over time. Metrics will be used to track things such as fuel consumption, age of the machinery and vehicles, toxic emissions, and packaging waste. In the future, these metrics will be used to provide a more sophisticated method to rate how planet-friendly the shipment of goods will be.
Not Just for Tree Huggers
Even the most profit-driven executives are finding that green agendas aren’t only for tree huggers. Cost savings from green initiatives improve their bottom line, and green practices are increasingly being scrutinized by customers as an indicator of their value as a business partner.
The two areas where companies can make a big difference are to put systems in place to help analyze their transportation options daily, and to use demand-based systems to better manage their forecasts and replenishment needs.
It’s all a matter of commitment. How green do you want to be?
Tom Kozenski is VP of Product Strategy at RedPrairie, and is focused on Commerce in Motion – developing software that moves raw materials to finished products to ensure visibility, collaboration and velocity between manufacturers, distributors, retailers and customers. More information at www.redprairie.com