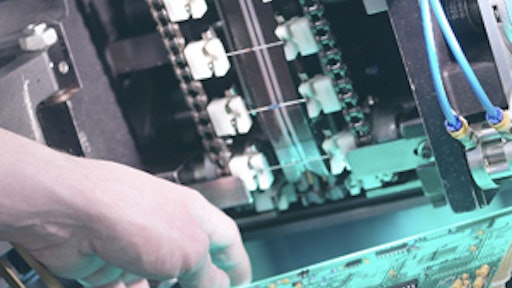
By Matthew Bather
Faced with tighter margins and increasing competition, manufacturers today are embracing innovative new ways to take plant floor automation and business management to the next level. Intelligent numerical controls are being implemented to drive efficiency on the plant floor. These tools monitor and measure the output of production data, such as job starts, machine hours and part counts, without manual intervention, pulling data directly from the machines on the plant floor. With all this data, however, the question arises: How should manufacturers use this information to drive productivity and profitability to greater heights?
Making the Data Work for You
First, businesses must move beyond the "silo" approach of the past and share this shop floor information across the organization. While enterprise resource planning (ERP) has helped to automate individual departments, it hasn't extended its back office benefits into the front office where there are tremendous opportunities to better manage people, workloads and supply chain issues. In fact, ERP implementations typically only penetrate 15-20 percent of an organization. Today's business leaders need real-time insight into their entire business, without being bogged down with added time to consolidate data and generate reports. They need to view current metrics on a continual basis to monitor the health of their business. Organizations that continue with traditional ERP deployments without the benefit of full operational integration will struggle.
Realizing this limitation, many companies have embraced the concept of extended ERP — incorporating capabilities such as customer relationship management (CRM), human resources management (HRM), knowledge management and workflow management along with the traditional materials planning, distribution and order entry functionality. This enables the free flow of information to appropriate parties for more informed decision-making.
Extending ERP requires adopting a new mindset whereby all facets of the value chain are interconnected. This means breaking free of the old methodology of preserving data in individual fiefdoms and learning to share information within a rules- and role-based system. For example, production data coming directly off machines can be integrated with an ERP system so that job shops always have the most current data, enabling them to better control headcount and costs.
Access to this production data along with employee information and other operational data should be in a single system in order to more effectively manage production. Such integration provides a more holistic view of the organization from the plant floor to the top floor, ensuring that business runs smoothly and customer expectations are met. Imagine the possibilities of always knowing exactly which jobs are in process, how much inventory is in stock, which products are most in demand and how much staff you'll need at any given time. By linking traditional ERP with advanced tools that help run a business, organizations gain a unique ability to see where processes intersect and how they impact one another, identifying levers of change that will garner the best result. This clearer picture of the business can lead to tremendous cost savings and operational efficiencies.
Extended ERP also requires a powerful workflow component. This doesn't mean a crude "send"-only model such as e-mail, but a business rules-driven system that automates the flow of communication and tasks. This comprehensive approach ensures that assigned tasks are completed or elevated automatically to the next level should a problem arise. Workflow functionality can be used in conjunction with advanced alert management technology to make certain that any potential issues in the production chain do not become a crisis.
Applying the ConnectionThe following scenario shows the importance of correct application and integration of intelligent numeric controls with other management systems. A salesperson or customer service representative fields a call from a customer and is asked the question, "When is my order/job due to ship?" or "What is the status of the order I placed with you a few days ago?" These questions relate back to work being done on the plant floor and information managed on the top floor, and without integration, the rep would have to either access multiple systems or ask another employee for the answer. Having a single source of information, on the other hand, enables that rep to easily pull up the customer account and locate the answer. As a result, the business is able to operate more efficiently, and employees are better able to serve customers.
Extended ERP is also particularly useful for better inventory management. A brake piston and pulley manufacturer, for example, streamlined manufacturing processes such as pick ticketing, traceability and bill of materials. The company found the new, fully integrated technology beneficial as it implemented a Lean philosophy. The firm attributes this to the reduction in the number of days of inventory and a reduction in order cycle time. Today the manufacturer plans its inventories based on accurate forecasts available via electronic data interchange (EDI) from automakers. Customers might place an order on a Monday and require a specific quantity of parts the following week, and the amounts vary drastically. Gaining access to just-in-time forecasts ensures that they don't run out of any given product, and they are able to turnaround orders more quickly to meet the needs of the most demanding clients.
In another scenario, a well-known supplier of instrumentation and control products implemented an extended ERP solution to differentiate itself from competitors in a commodity-based hardware business. By connecting CRM, HRM, supply chain management, document management and workflow tools, the company gave its suppliers and customers the ability to communicate with ease. More importantly, the firm gained a more comprehensive view of its customer account management cycle. Using business process tools, the firm mapped its sales cycle to a practical and efficient workflow, ensuring that each opportunity is continually maximized. The company credits the extended ERP solution with raising profits and sales to record levels.
These manufacturers understand a common theme: Fully integrating the plant floor with the top floor breaks the barriers to accessing the full capabilities of ERP systems and creates 20/20 vision throughout the company. As manufacturers have broadly adopted ERP systems, effectively extending and leveraging its full value are the keys to keeping a competitive advantage within the industry. As with any industry, early adopters have the potential to stay ahead of the curve. Manufacturers that have responded to the call of extending ERP possess the ability to analyze data coming from the plant floor and functional departments at the business level. As a result, these manufacturers derive key performance indicators (KPI) that monitor operational efficiencies and the bottom line. By connecting all facets of the organization and utilizing workflow tools that optimize each business function, these companies are achieving unprecedented levels of visibility and efficiency within the organization.
The Next Technology Frontier
Business in the 21st century is complex, fluid and customer-centric. It requires stringent, yet flexible processes and communications systems that extend globally and respond instantaneously. The processes and systems must be integrated. No part of the enterprise can escape the pressure to deliver measurable results.
RP gave businesses a vehicle to manage information and use it to their advantage. It organized customer data in ways that helped individual departments operate more efficiently, and it created streamlined processes that helped manufacturing operations cut costs and move products along more quickly. But traditional ERP systems failed to complete the task they ultimately set out to accomplish: to unify the enterprise and turn it into one smoothly running machine.
The next generation of extended ERP solutions promises to bridge this gap. New software tools are available that link departmental communications, work processes, customer data and supplier capabilities into a centrally functioning system, all focused on driving the enterprise forward. Challenges do remain. Companies will continue to face barriers as they revise internal processes, open up communications to outside sources and integrate disparate technology functions. But the move toward the next technology frontier is under way, and the enterprise will benefit as changes are made.
About the Author: Matthew Bather is product marketing manager at Exact Software, North America. More information at www.exactamerica.com.