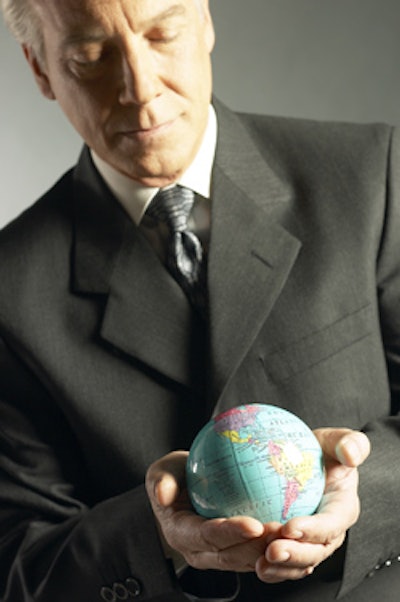
All the world supports green supply chains — until they cost more than alternatives. The key to making them deliver like Wal-Mart's supply chain, saving an estimated $3.4 billion in 2008, is an emphasis on practicality and structure. Effective supply chains accommodate a wide range of unforeseen issues and events but are otherwise highly structured, well planned and effectively synchronized. How can your supply chain deliver similar results on a percentage of revenue basis?
Start with a simple stratification of sourcing activities into: raw material, production, packaging and transportation/logistics. In each of these categories, there are choices that can lower your cost, enhance your revenues and polish your green image so that your customers believe in your corporate commitment to environmental responsibility.
Evaluate your raw material choices (or your suppliers' choices) so that you are selecting renewable, sustainable or recyclable materials, and choose materials that can be sourced close to your manufacturing facilities. Many companies find that there are additional revenue streams in recycling that can offset initial material costs.
Look at both manufacturing processes and the factories that implement them. Simple analysis of process steps, workflow and opportunities for parallelization in otherwise serial activities can diminish the energy, labor and material needed for production. Is the factory using energy-efficient lighting, low-cost labor, efficient processes or advanced methods? You also can help your suppliers choose manufacturing approaches that mirror your priorities and provide incentives for behavior that fulfills your energy and cost objectives.
Once goods are produced, packaging must be selected that has endured a thorough reevaluation. Few marketers considered energy efficient and environmentally sensitive packaging years ago, and yet there are many savings to be found here, often simply through better organizational communication. Do the stores really want one item per poly bag, or do they take them out upon product arrival, with great time and labor expended? Does the product need to be encased in nuclear-hardened polystyrene or could it be packaged more sensitively? Can the goods be prepackaged at production and more effectively shipped in bulk, with some final packaging to occur at the distribution center (DC) or store? This isn't rocket science, but it does take a rational, ordered approach to properly advance the state of the art for your unique business.
Lastly, look at today's fuel costs and recognize that they are built into everything you source globally. Many firms are looking at "near-sourcing," which simply means looking at suppliers with geographical proximity — in the United States, these are Canada, Mexico and the Caribbean/Central American countries, and, to a lesser extent, South America. Europe is already sourcing heavily from Eastern European countries and other Europe/Middle East/African (EMEA) nations. The world sources from Asia/Pacific Rim countries, but transportation costs, duties, port congestion and timing challenges can tip the balance and make alternative sources more attractive.
At the end of the day, even a cursory evaluation of these categories will likely produce measurable benefits to your agility, green score and bottom line. Because after all, we all want a green supply chain that delivers every kind of green.