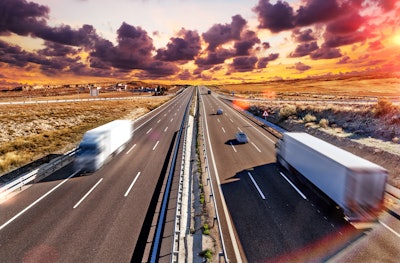
Lean and its just-in-time (JIT) manufacturing philosophy (or tool) has had a tough time in the press in recent months, as it has been blamed for causing the current supply chain crisis. How? This methodology has led manufacturers to keep just a bare-bones inventory of raw materials and components, which left them high and dry when the pandemic temporarily shut down their supply chains and threw the balance between supply and demand into disarray.
Lean and its just-in-time philosophy do help manufacturers develop an extremely lean supply chain, which, as long as everything runs as expected, does enable organizations to keep inventories very low. But lean does not require this. In fact, it recommends retaining a critical reserve of key components and materials strategically placed in the supply chain to prepare for just this kind of crisis.
Additionally, Lean encourages organizations to shorten the supply chain so that it’s easier to manage. An organization that’s outsourcing key business processes to offshore companies may be making a good decision for their cost management, but they're not following lean principles. Offshoring key business processes leads to a loss of control over the supply chain.
That said, Lean creates highly efficient organizations, which presents a very tempting proposition to senior management: keep inventories low to reduce working and boost profits. Unfortunately, that strategy results in a short-term gain at the expense of increasing long-term risk, as many have discovered in the last two years.
Lean’s origins: Maximum value from scarce resources
Anyone who’s studied the origins of Lean won’t be surprised that the methodology does not encourage extremely low inventories. Originally developed at Toyota during the postwar period, Lean was a response to shortages of raw materials in Japan. The goal was to make the best use of the scarce materials that they were able to procure by only making a product when there was confirmed demand for it.
So, it’s not a coincidence that Toyota hasn’t been hit as hard as other car manufacturers due to a lack of parts during the pandemic. The automaker learned its lesson more than a decade ago, when the 2011 tsunami triggered the Fukushima Daiichi nuclear disaster. The catastrophe made it hard to find key parts, which triggered production slowdowns. “Never again,” Toyota said, so they mandated keeping a six-month stockpile of 500 critical parts.
That policy has served them well, enabling them to continue limited production while their competitors had to slow operations down significantly.
Underlying causes of the supply chain mess
The supply chain crisis we’re experiencing has roots that delve far deeper than the emergence of COVID-19. The pandemic, along with the U.S.-China trade war, exacerbated existing weaknesses beyond the breaking point of most supply chains, resulting in the current crisis.
Over the past decade and a half, container ships have increased in size by 250%. It’s more cost-efficient to consolidate loads in one large ship than in multiple smaller ones, but these ships are too big to pass through the Panama Canal. As a result, goods arrive from Asia on the West Coast of the United States and are then shipped largely by truck across the country. It’s far shorter and less expensive than going around Cape Horn.
With the easing of public health measures, demand for goods in the United States skyrocketed, which created enormous queues of container ships that have had to wait up to two weeks to dock at major West Coast ports. Compounding the problem is a nationwide shortage of truck drivers. Logistics companies downsized during the early part of the pandemic when demand fell, and they’re now struggling to scale back up.
And that’s not all. U.S. manufacturers are still ramping up, which means there’s little to ship back in those empty containers. It doesn’t make financial sense to ship empty containers, so they remain in the U.S., which has caused a shortage of containers in Asian markets.
The shipping companies have also contributed to the problem by reserving almost all capacity for their most lucrative routes which has contributed to a clogging up of these routes while the less lucrative routes are currently unserviced.
How lean and just-in-time can mitigate the current crisis
Thriving during the current crisis requires a fundamental understanding of demand (especially its drivers), inventory and the supply chain to the highest degree possible. Understanding exactly what your customers need and not just what they want, because in a situation of uncertainty, companies will secure as much of a resource as possible in case it’s suddenly in short supply. ERP platforms that are purpose-built for manufacturing can be integrated with analytics and AI software can do exactly this.
Next, leverage Lean practices to get every bit of value from the raw material you have, making products only when demand exists. Move from a “push” to a “pull” system. ERP can assist here, too, so long as the platform has strong supply chain and inventory management capabilities.
Finally, invest in technologies that will make the company stronger when we emerge from the current supply chain morass. This means improved collaboration and communication throughout the business, especially with improved communication. Dual sourcing, for example, can provide much-needed supply chain resilience, but with proper control mechanisms because it quickly becomes very complex.
In these times of uncertainty, many manufacturers don’t know when they’ll get the raw materials they need, nor when they’ll be able to deliver products to their own customers. Lean and JIT are not the problem, yet used correctly, can produce unique solutions and solve a number of the current problems. Coupled with the right technologies, these methodologies can help manufacturers weather the storm to come out stronger on the other side.