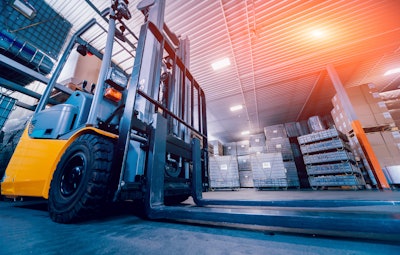
As a wave of in-person events flood our calendars, I’ve observed a distinct shift from pre-pandemic expectations from these interactions. The need for automation has become more exacerbated during COVID lockdown challenges. Throughout the global pandemic, the need for automation has outpaced the solution cost. As a result, solution providers that remain focused on solving real world problems, offer unbeatable customer service, and continue to improve the sophistication of their technologies, will win more business. As the post-pandemic supply chain shows no sign of slowing down, it is palpable to hear the urgent need to solve the growing logistics problems for ecommerce and logistics brands.
Flexible AI for next-level operations
Mechanical solutions have taken the industry a long way in terms of fulfillment center and parcel sortation center automation. While these systems aren’t necessarily reaching the end of their capability, the amount of room these systems take up and the amount of throughput per square foot and outputs they provide are limited in volume. When you consider the millions of destinations that exist for parcel delivery, there is room for new automation to catapult the output capabilities.
For example, consider an adaptable sorting system that handles immense volume for a high-density zip code with many packages. One sorting system might manage one zip code, while another handles multiple zip codes where each bin represents one unique location. This vector of volume and number of ultimate destinations is a never-ending math equation. Expanding the capability of the mechanical solution with a combination of mechanical and autonomous technologies opens the door to new throughput capabilities, not to mention reducing operating costs upwards of 40%.
In this world of increasing complexity, off-the-shelf robotics will not work for every business. Sourcing adaptability within your AI solutions is critical to providing the flexibility, scalability, and configurability that is more attractive now than ever before.
The ripple effects of putting people first
Employees have so many more choices now when it comes to their employment. Employers want their employees to be delighted to show up at work and employers should protect their associates as assets just like they would protect the physical assets in the warehouse. For example, focus on safety and prove to your associates how much they are valued. Employees pay you back in a way other assets cannot, and providing them opportunities to learn new skills helps elevate the working conditions. This leads to happier employees who want to grow with your business. Automating simple tasks like sortation gives the team back time to focus on “human-level” tasks.
Optimizing reverse logistics
As more people shop online and purchasing shifts from brick and mortar to ecommerce buying, the product returns game grows exponentially. Unfortunately for those in the returns business, most automation solutions are geared toward forward logistics.
When an item is returned and goes back into the fulfillment network, a variety of steps take place to return the item to its homogeneous state or that ensue to filter the item through the fulfillment partner to its origin point. Typically, a central return point acts as a middle ground before forwarding the parcel to the correct end destination.
We expect to see more companies fine-tuning their reverse logistics, which we know comes with an upfront cost. However, leveraging automation within the four walls of the warehouse unlocks access to more last-mile opportunities. The reverse-logistics landscape is challenging, but the competition is minimal…for now.
Increasing throughput per square foot to reduce capital expense
According to Digital Commerce 360, the pandemic contributed more than $218 billion in ecommerce sales in the past two years. Increasing efficiency is always on-trend, and optimizing sorting to move more parcels in less space will continue to reign.
As the autonomous systems create more density in volume flowing through the network, warehouses require less space and have fewer trucks on the road. Shippers accomplish this by packing more per truckload to alleviate void truck space. Global shipping companies are reaping the benefits of sorting automation in their transportation cost savings up to 20%. Deploying AI-powered horizontal putwall systems, this automation is driving value by increasing the per-mail-sack package density by up to five packages per sack. In turn, this has reduced the number of truckloads per day leaving the warehouse.
With efficiency comes an offset in capital expenses. Before spending money on new facilities, automation is empowering companies to maximize existing facilities first. Automation maximizing each square foot helps decrease the need for new construction or additional warehouse space as consumer demand continues to boom. The offset causes a ripple effect and businesses may be able to avoid spending capital on concrete and instead invest in their people.