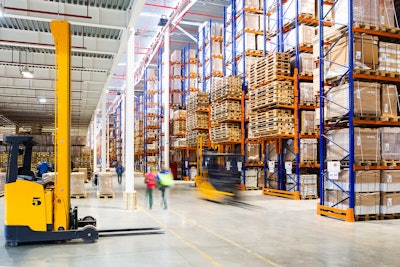
In early 2020, the world literally changed overnight, forcing everyone to quickly adapt. Our expectations as consumers were high. We could order any product and get it the same day or at most, a day or two later. Shelves were full and shortages rare. But that changed quickly and those days of immediate gratification are not coming back anytime soon.
The harsh realities of today's supply chain disruptions are wreaking havoc with the ability of manufacturers and retailers to keep up with customers’ expectations and demands for more complex products. The selection of new cars is still limited, with waits of several months to get the color or model you want. New windows can take upwards of 20 weeks from order to installation. Low inventory of parts leaves those with broken dishwashers hand washing their dishes until repairs can be made.
There seems to be no end in sight for returning to what we all thought normal was just two years ago. Several factors are creating this perfect storm. The initial closing of factories in Asia in early 2020 created a product domino effect that we continue to experience. Many factories are still working at limited capacity as a result of COVID-19. Chip shortages persist, impacting production of everything from robotic vacuums to vehicles and creating delays that are not getting shorter. And container ships continue to stack up at many major U.S. ports, waiting several weeks to offload their cargo.
Many of these supply chain problems are outside of the control of manufacturers and retailers, yet they have a significant impact on these companies’ bottom line. One study in 2021 revealed that a single supply chain disruption of any kind caused an average 4.82% decline in sales, while operating income dropped 26.5% and returns on assets (investment) fell 12.7% during the three months after the incident took place.
So, what can be done to protect against these adverse effects? It all comes down to infrastructure, employment and innovation.
Improving infrastructure
Nearly two years later, there are still dozens of ships waiting in the waters outside of major West Coast ports to offload containers of goods from Asia and Europe. The supply chains have ground to a halt in the U.S. because ports do not typically run 24/7. They aren't nearly as efficient as their counterparts around the world, either, since they lack the same high level of automation. Additionally, the customs officials who are needed to clear and admit the goods only operate on a standard typical Monday-Friday, 8 a.m. to 4:30 p.m. work schedule.
The recently passed $1 trillion Infrastructure Investment and Jobs Act hopes to address these issues and more. The Act allocates several billion dollars to initiatives designed to remedy supply chain challenges, minimize disruptions to global commerce and speed products to consumers. Specifically, about $17 billion will be spent on efforts to modernize and expand ports. And in late February, the U.S. Department of Transportation issued requests for proposals for $450 million in grants through the Port Infrastructure Development Program, with the intention of expanding port terminals, piers, rail yards and storage facilities.
Recent legislation also has earmarked money to upgrade our digital infrastructure. Strengthening our security to prevent cyberattacks is critical since ransomware attacks and hacking are growing in frequency and causing significant disruptions to business operations.
Employment incentives
The Great Resignation is causing labor shortages in all sectors. About 75% of CEOs believe that a shortage in skilled labor is the most likely external issue poised to disrupt their business in the coming years.
Consider trucking. This $791.7 billion industry hauls 72.5% of all freight transported in the U.S. and employs about 6% of all full-time workers. The ongoing truck driver shortage is now estimated at 80,000, up from 61,000 just three years ago. And, the industry will have to recruit 1 million new drivers within the next nine years to replace those who are retiring, a new study from the American Trucking Associations (ATA) estimates.
eCommerce and order fulfillment centers also are strained as they struggle to find enough employees to handle the increasing number of orders and quickly and efficiently pack the products to get them to consumers. A 2021 Inbound Logistics 3PL market research report found that 47% of shippers and 73% of 3PLs report that finding, training and retaining qualified labor is one of their top challenges. All totaled, almost 70% of warehousing and transportation businesses told recruiting company Manpower that they have trouble hiring skilled workers.
Technology innovation
Companies need to reimagine supply chain planning to better support lean manufacturing and "just-in-time" production that have become accepted practices. The key is to leverage new technologies - cloud computing, artificial intelligence, machine learning - to better align strategy, people, processes and data to business objectives, and connect data from diverse sources for seamless planning with greater frequency and accuracy.
In a world where supply chain decisions need to be made rapidly with live information, spreadsheets no longer can support a company’s dynamic needs. Chasing and reconciling data wastes valuable planning time. Companies on the front lines of supply chain innovation are moving to solutions that give all participants a single source of truth that can be adjusted on-the-fly as factors change.
When new technologies are applied, there can be a dramatic impact. Consider the experience of Wright Medical, a global medical device manufacturer that is now a part of Stryker. The company’s integrated business planning (IBP) processes would typically take almost three weeks. After transitioning to an always-on planning environment, which integrated live information from diverse sources, Wright Medical was able to garner real-time insights for forecasting and have greater visibility for demand modeling. The results were impressive: the monthly IBP process dropped to just 5 days and forecast accuracy improved from 60% to over 85%, with forecasts for many products hitting the company’s accuracy target of 90%.
As we adjust to our new post-pandemic reality, we cannot afford to rely on the same strategies and tactics that have worked well in the past. Companies that operate along every step of the supply chain will need to be proactive and take the necessary actions to address an ever-changing marketplace. While the focus and funding by policy makers is a good start in improving the infrastructure that supports the supply chain, those businesses working within the supply chain will have to take action - from addressing employment shortages to leveraging innovation - to overcome today’s challenges and build a foundation for success in the future.