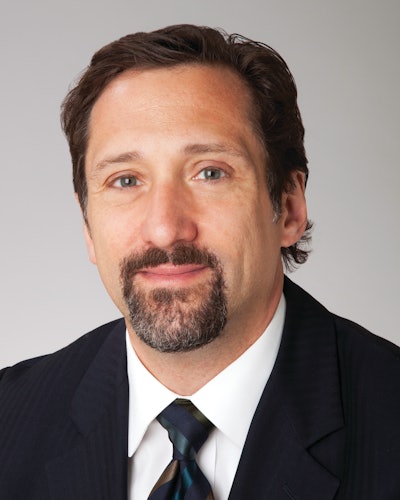
Are businesses prepared to cope with today’s world?
To paraphrase Lewis Carroll: If you don’t know where you’re going, any road will get you there. But the opposite is true as well: If you know where you’re going, some roads are better than others. And you need to figure out which ones are best. In the current business environment, with its ever-increasing complexity and growing interdependence, knowing where you’re going is the only way to cope—and ultimately thrive. Therefore, the more thoroughly companies understand potential risks to their supply chain, the more likely they will meet or exceed financial and strategic goals.
In Carroll’s Through the Looking Glass, many things in the mirror were the opposite of real life, such as clocks running backward. As used in the book, Alice goes through the looking glass to find a world both clear and recognizable yet turned sideways. Thus, through the looking glass is extended as a metaphor into any time the world turns strange, or when things get turned around, as if one were Alice, inside of the mirror.
Similarly, in today’s global business landscape, viewing the supply chain as a set of tangible assets and related liabilities to be managed and insured is no longer realistic. Rather, increased risk exposure requires a holistic risk management program that focuses on an organization’s network of assets—both internal and external—across all operational functions. Such an approach allows supply chain managers to make better and more informed distinctions between the competing priorities of process cost-effectiveness and controlled efficiency of enterprisewide risk exposures. An organization’s supply chain can’t be considered optimized simply because it’s efficient and cost-effective; it also must be risk-adjusted, factoring risk into supply chain decision-making.
A comprehensive supply chain risk management strategy—and the incorporation of an array of predictive analytic tools to measure and manage risk—is now a central component of any risk-adjusted supply chain and often extends beyond the supply chain itself to encompass all major operations of the organization. In fact, modern predictive analytics is fast becoming a tool to recognize key trends, patterns, and potential disruptions within supply chains and a means to protect the enterprise’s most valuable assets while also creating sophisticated risk mitigation models.
The devastation from major catastrophic events can disrupt supply chains locally and worldwide, in turn causing significant repercussions in the global economy. Organizations that employ analytics and innovative weather intelligence can mitigate the costly effects of such events. Analytics can help manage regulatory compliance such as environmental health and safety (EH&S) and sustainability across supply chains and product life cycles. EH&S analytic tools present a comprehensive view of relevant trends, and the resulting business intelligence enables more effective management of product stewardship and workplace safety regulatory requirements. Predictive algorithms can alert supply chain managers to major issues in operations and processes. Companies can also apply predictive analytics to historical cargo theft data to plan the safest routes for the transport of goods.
A primary concern of supply chain and risk managers alike is supply chain disruption. Interference in materials production or delivery can lead to lost sales, decreased revenue, margin erosion, profit loss, and damage to reputation within the marketplace. Effective disruption mitigation requires thorough risk analysis at each origin, intermediary point, and transportation link. Managers can thereby see all key areas of potential harm and determine how best to allocate resources to protect against vulnerabilities.
Managers must work closely with supply chain partners and corporate compliance professionals to improve collaboration, create a risk mitigation plan, and install a contingency protocol across the network. Supply chain managers need to know where the organization’s supply network begins and determine who controls the various origin points.
But risk assessment doesn’t end at origin locations. Each intermediary and throughput location—distribution center, warehouse, rail terminal, truck stop—has logistics operations and potential risks that must also be considered. As they do for suppliers and origin locations, supply chain managers need to identify who controls operations at each intermediary point to understand information regarding efforts to lessen the potential for disruptive risks.
Depending on the nature and location of the operation, disruptive risk can vary. Political turmoil can cause concerns about port security and volume flexibility. Intermediary points are also vulnerable to cargo theft, a risk that costs the U.S. economy billions of dollars each year.
With requirements constantly changing and product inventories in motion, companies must track hundreds of regulations in numerous jurisdictions as they apply to thousands of products. Comprehensive, centralized global regulatory intelligence can help ensure overall product and facility compliance. Analytics can support product and material regulatory research, data management, decision support, and compliance initiatives.
Developing and maintaining a reliable, resilient supply chain is vital to the success of any business, particularly in today’s economy. Increasingly, supply chain and risk managers are working together to identify and mitigate the risk of disruption along all points of the supply chain. As sophisticated technologies such as predictive modeling and weather intelligence continue to evolve, organizations that adopt such tools will be well positioned not only to protect their most valuable assets but also gain a key competitive advantage.
How can companies begin a supply chain initiative? An effective supply chain risk management strategy involves finding and prioritizing vital business components, charting the full supply chain to highlight interdependencies, and uncovering areas along the supply chain where disruption can lead to failure. Or to paraphrase Lewis Carroll once more: Begin at the beginning and go on till you come to the end; then start again.