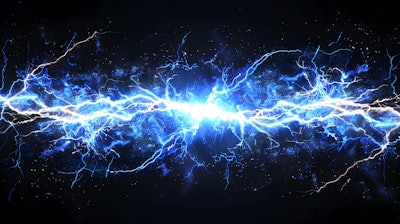
For businesses, pressure is mounting to move toward a more sustainable future. Green-focused targets have been embraced by governments worldwide, such as the U.S. aiming to cut greenhouse gas (GHG) emissions in half from 2005 levels by 2030, and the European Union raising their binding renewable energy target to a minimum of 42.5% by the same deadline. Additionally, corporate initiatives, employee health and safety concerns, supplier mandates and consumer and investor behavior are compelling operations to consider their impact on communities and the planet.
Supply chains have a critical role to play in these efforts. An organization’s supply chain often accounts for more than 90% of its GHG emissions. Electrification—the process of substituting electric power in place of fossil fuel sources—is a particularly meaningful opportunity businesses can act on to further their decarbonization efforts.
Today, electrification is an option even in intense industries such as lumber, agriculture, steel and ports. Viable electric alternatives are available for high-capacity equipment like heavy-duty forklifts and even container handling solutions. But, before deciding whether to electrify, it’s important for operations to consider their priorities and evaluate them against the available clean power options.
Electrification Without Compromising Performance
Leaving behind internal combustion engine (ICE) power in favor of electrification does not mean sacrificing productivity:
- Performance – Electric power can deliver the performance operations expect from ICE and can operate effectively in applications that require long runtimes.
- Reliability – Electric drivetrains have fewer components and less complexity than ICE options and offer similar or better reliability with reduced maintenance.
- Infrastructure – Governments and businesses are increasingly investing in the infrastructure necessary to support electrification.
- Cost – Electric options can help reduce costs related to fuel consumption and engine maintenance, and incentives, grants and offset credit programs are available.
Of course, performance is only part of the equation. Factors like local utility grid capacity and run time requirements come into play, because time spent charging or refueling equipment must not negatively affect operational schedules. For example, areas with weak electric grids can experience brownouts that can slow down operations and disrupt carefully timed charging schedules.
Available Power Sources
Unlike lead-acid batteries, today’s lithium-ion batteries can deliver the ICE-like performance that high-intensity operations require. Lithium-ion technology also provides greater energy density, power transfer and service life.
Lithium-ion batteries are powering lift trucks of increasingly high capacity. Starting in 2020, counterbalanced forklifts with integrated lithium-ion power in the 15,500- to 19,000-pound capacity range became available, and models capable of handling even heavier-duty applications with capacities of 23,000- to 36,000-pounds hit the market the following year.
Today, electric power sources are taking on even higher-capacity equipment, especially in port settings where electric container handlers, ReachStackers and terminal tractors are in pilots or under development. Such equipment is powered by either a lithium-ion battery or hydrogen fuel cells (HFC):
- Large lithium-ion battery — This approach offers choice between conventional, and opportunity charging and is designed for a medium-duty cycle.
- Hydrogen Fuel Cells — This approach offers the ability to refuel the truck with hydrogen (in a manner similar to diesel) in 10-15 minutes, and stands up to a heavy-duty cycle, enabling operators to work a full shift without stopping to charge or refuel.
Equipment powered by HFCs combines the simplicity and sustained performance of ICE with the zero harmful emissions and reduced maintenance of electric drivetrains. An added benefit is the speed with which they can be refueled, with no downtime for battery changing and charging.
What Does Electric Mean for Operators?
Of course, emissions reduction and strong, sustained performance are not the only benefits for intense applications exploring electrification.
Many operations are struggling to recruit, train and retain sufficient labor. And with demanding duty cycles and inhospitable environments pushing both equipment and operators to their limits, businesses need to consider equipment with attributes that help operators perform at their best. Electric equipment can be part of the answer to maximizing the efficiency and productivity of operators and their time.
Reduced charging or refueling time, fewer maintenance requirements and easier serviceability can all add up to operators spending more time working and less time waiting. Electric trucks can also support a work environment that can offer greater operator comfort and performance. With no internal combustion engine running, truck noise levels and vibration are reduced, and there are no tailpipe emissions. The reduced maintenance workload associated with electric trucks can also be an important aid for businesses struggling to source technicians from a tight skilled labor pool.
Ergonomic fundamentals like visibility and operating position remain primary factors for electric lift trucks. Whether electric or ICE-powered, features like visibility, easy entry and exit, ergonomically designed cabs and easy access to controls and information are important considerations.
Charting an Electric Future
Many operations are already making the shift to electric. In 2023, adoption reached an all-time high, with electric accounting for more than a third of all sit-down counterbalanced forklift purchases – an 8% increase in a single year – according to Industrial Truck Association (ITA) factory booking data. Electrification is a realistic option to not only satisfy the business requirements and operational needs for increasingly heavy-duty applications, but also to help support decarbonization and sustainability initiatives.