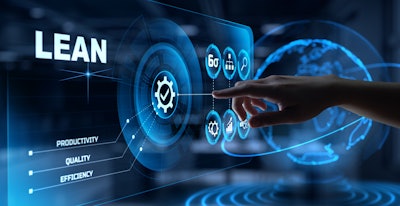
The term “Lean” has been around since the early 1990s when it was mentioned in the book, “The Machine That Changed the World.” With over 30 years of existence, the definitions and understanding of what Lean is are extremely varied. For those who have spent their careers understanding and using it to drive operational excellence and growth strategies, it is a pivotal concept. When leadership and vision align with Lean as a key part of an operating system, organizations achieve results that are second to none and develop their teams to solve problems at an accelerated pace. It has been and can be used in any process, such as continuous manufacturing, discrete manufacturing, metals and pharmaceuticals, as well as any organizational setting, such as shopfloor, office, warehousing, engineering, purchasing and healthcare. It can also be used in any idea or concept, such as environmental, social and governance (ESG) and strategic development.
What Is Lean?
On the surface, Lean is very simple to understand. It is about correctly identifying the steps required for a customer to complete a process – otherwise called the customer’s value stream – and determining what steps add value in the eyes of the customer and what steps do not. Non-value-added activity is considered waste because it is something that a customer is not willing to pay for. Customers, whether internal or external, are not interested in the problems and inefficiencies that a supplier or supplying process has; they want the product or service, issue-free, when they want it. This is when individuals and teams begin to drive continuous improvement to eliminate or reduce the non-value-added activity within a process.
This may take multiple attempts through projects or Kaizen improvement events, with the most mature Lean organizations espousing small improvements every day. As waste is eliminated or reduced, the time it takes to complete a process value stream begins to compress and as process lead time shortens, that process can produce more goods or services to sell. By eliminating the waste, the faster cycle creates growth opportunities to sell the additional output without increasing the workload for facility associates.
What Is Waste?
We have determined that waste is something the customer does not want to pay for, but what exactly might that be? The term Lean was really an attempt to describe the Toyota Production System (TPS). One of the tenets of TPS was to understand the eight forms of waste: correction, overproduction, material movement, motion, waiting, inventory, processing and defects.
- Correction – Correction is the process of addressing a defect or issue. The additional steps to correct issues are waste because the cost of the process increases with each additional step.
- Overproduction – Overproduction is creating more product than necessary. Overproduction increases risk because if demand suddenly decreases, cost will be tied into something that may not be easily or quickly recuperated.
- Material movement – Material movement involves moving materials from one place to another. While materials sometimes do need to be moved, the product is not being changed or transformed by a value adding activity. Movement should be minimized as much as possible where value is not being added.
- Motion – Motion is focused on the movements of people and machines. Is there wasted time in the steps of a process? What can be done to improve or eliminate them?
- Waiting – Waiting is the opposite of motion. It focuses on the amount of time people or machines must wait during a process. Consider how you can decrease waiting time in processes to make them more efficient.
- Inventory – Excess inventory is one of the most detrimental forms of waste. If a facility orders or manufactures too much of the wrong product, they will face challenges such as having product that might not sell, paying the carrying cost to finance it, having insufficient room to store it and losing demand for it before it can sell.
- Processing – Processing involves any extra step done to a product that the customer is not willing to pay for. In order to provide great products and services, you must truly understand what the customer believes is valuable.
- Defects – Defective products create waste by sinking cost into a good or service that is faulty and cannot be used. Defaults increase costs by having to repair the product.
How to Reduce Waste
Once you understand what waste is, you can begin to identify it and work to eliminate or reduce it in you enterprise. There are several steps that can be taken to reduce waste and become more Lean as an organization.
Value Stream Map
One tool for eliminating waste is a value stream map. A value stream map documents the current state of a portion of your value stream. It is a visual representation of the steps in either all or part of the process that you want to better understand. Key aspects required to understand a process include cycle times of each step, how information is used to drive activity in the process and the amount of inventory queued up at each step.
Takt Time
To further minimize waste, it is important to understand what the true customer demand is. To do this, you can calculate a number called Takt Time, which is the rate at which a customer needs a good or service supplied to them for a given time period. By using this method, a process can be created to use the least resources necessary – man, machine or material – to meet the customer’s needs and benefit the organization.
Lean Concepts and Activities
Once the Takt Time is established, organizations can implement concepts like Kaizen, Single-Minute Exchange of Die (SMED), 5S, Total Productive Maintenance (TPM), Problem Solving (5-Whys and Fishbone diagrams) to improve the value stream through the issues identified.
- Kaizen – A process for eliminating waste, improving productivity and enabling continuous improvement.
- SMED – A process enabling change-over from one product to another in equipment or processes.
- 5S – The 5s process (Sort, Set-in order, Shine, Standardize and Sustain) creates a high level of workplace order, safety and efficiency.
- TPM – TPM is a system that promotes and creates consistent predictable maintenance work instead of reactive work.
- Problem Solving – Problem solving involves documenting the known information or issue and then using methodical approaches to develop solutions.
Lean, based on its ideas and the system needed to drive it effectively, is truly made to promote, create and sustain ESG. If an organization wants to drive the three pillars of corporate sustainability – the environment, social responsibility and economic benefits – Lean is already aligned to that. Using minimal resources to create products or services fosters organizational sustainability; showing respect for people by allowing everyone to solve problems, fosters social responsibility and creating success for everyone fosters economy. At its core, Lean pushes an organization to be more sustainable.