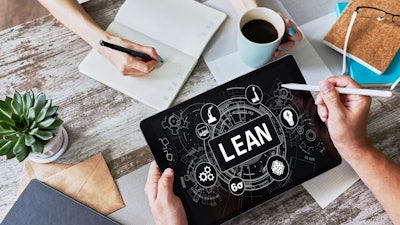
Companies continue to face supply chain disruptions worldwide and these disruptions and product shortages will likely continue throughout the year. While there are multiple factors contributing to these supply chain issues, one major factor can be attributed to the lean manufacturing methodology of companies keeping inventories intentionally lean to reduce costs. Under this system, new shipments and raw materials arrive just in time to fill a demand for new products.
The pandemic proved that existing methods for efficiency don’t necessarily translate into resilient manufacturing. Although lean manufacturing is highly efficient in the best of times, it’s also highly susceptible to disruption in the worst. During a global pandemic, for instance, the need for more resilient manufacturing is stark. Fortunately, efficiency and resiliency aren’t diametrically opposed. With the right technology, companies can enjoy the best of both worlds.
Operational flexibility is the missing link
In 2019, McKinsey conducted a study that examined the performance of companies following the financial crisis of 2008. It found that the most resilient companies did something different than the others. In addition to efficiency, they built their business models around financial and operational flexibility. By quarter one of 2008, they had cut costs by 1%, and by the time the crisis reached its trough in 2009, they’d boosted earnings by 10%.
Cutting costs and focusing on growth are the traditional pillars of resilience. Today, however, a new wave of resilient manufacturing has emerged in response to restrictions that were put in place at the beginning of the pandemic. The manufacturing workforce, supply chains, and product demand have all been affected by COVID-19.
In this new environment, being operationally and financially flexible is not enough. Before the pandemic, digitization was a huge accelerator to efficiency and resilience. Companies that digitized early could cut costs and increase revenues; now, they’re much further ahead than companies that are still struggling with resilience.
Being digital is a critical component of resilient manufacturing, which is why some newer manufacturers have been slower to feel the supply chain drag. In fact, many have grown significantly faster due to their heavy reliance on digitization. Tesla, for example, has been super resilient from the start, because the entire workflow is digitized, and its people know how to communicate with customers digitally — including taking, fulfilling, and delivering orders. In the industrial space, efficiency and resiliency are built by companies that invest in these same elements.
Why resilient manufacturing isn’t a lost cause
Resilient manufacturing is essential in the current environment, and building it will provide manufacturing facilities with significant flexibility beyond the pandemic. To create a complex lean manufacturing supply chain, things need to combine and work together in a highly efficient manner. Companies have to cut out the fat by optimizing every system for efficiency.
The assumption is that each component of a product will be delivered just in time for it to be assembled on the factory floor. When a local, regional, or global crisis introduces systemic risk to any part of the supply chain, that link in the chain is lost. The component may never reach the factory floor because optionality and buffers have been optimized out.
Manufacturers must combine lean manufacturing with resilient manufacturing methods. That requires a digital thread running through the entire operation, with end-to-end operational visibility across the whole supply chain. With greater visibility, companies can predict shifts in demand with much more flexibility.
Operational visibility also creates a wider base of optionality and suppliers. Digital visibility shows, in real time, what components or raw materials manufacturers need, how their supply chain is providing them, and what they’re manufacturing with them. Companies can efficiently switch suppliers or products in response to, or even before, major disruptions.
Operational flexibility combines efficiency and resiliency
For manufacturers to effectively combine efficiency and resilience, they need enough data, knowledge, and understanding of what their supply chains look like at any given moment. They can predict major events to reduce or completely avoid disruptions to their manufacturing processes.
To achieve this combination, companies need three important digital threads:
- Total visibility into financial and operational flexibility: The most important digital thread is a digital space where key people in the supply chain can see it all. They can understand demand and sale smetrics, as well as analyze production, physical assets, delivery networks, logistics, and supplier bases. Ensure that sales, marketing, production, and all other departments can see the same numbers in real-time and make decisions together based on that single truth. This will be the supply chain control tower.
- Real-time machine health monitoring in all factories: In a lean manufacturing model, efficiency is based on meeting production needs. As the primary source of that production, machines are a company’s biggest assets, and a company needs full visibility into its machines’ health and performance at all times. That includes predictive knowledge about how they’ll perform under different conditions. Machine health monitoring platforms can gather data from IoT networks and use AI algorithms to deliver predictive knowledge based on that data, creating greater visibility in every factory.
- Remote collaboration through a connected worker platform: How machines will perform under different conditions is an important aspect of operational flexibility, but most operations rely as much on people as they do machines. It’s just as important to know how employees will work together when they can’t be near one another. Connected worker platforms allow them to work remotely, collaborate, and share operational data and insight so they can become more autonomous in the face of disruption.
Lean manufacturing methodologies have traditionally lacked this level of visibility, insight, and flexibility, which hindered many supply chains amid the pandemic. By introducing technology to boost real-time visibility and remote collaboration, however, companies can combine lean manufacturing efficiencies with an unprecedented level of operational resilience.