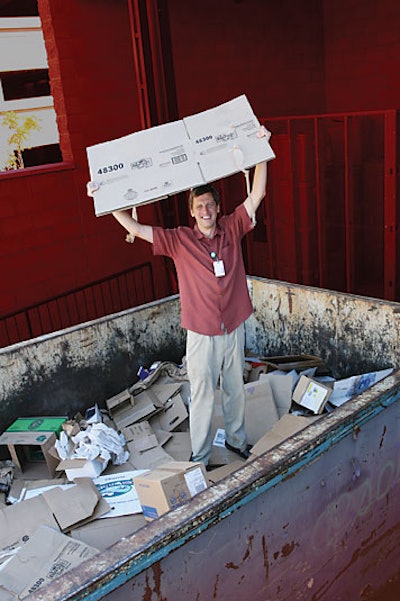
Kai Abelkis believes that going green doesn't mean going into the red. As the environmental coordinator at Boulder Community Hospital (BCH) in Boulder, Colo., Abelkis heads a program to find ways to "reduce, reuse and recycle" goods and materials procured by the hospital's 2,675 employees. These efforts have helped save more than 50,000 trees while eliminating 61,700 pounds of pollutants and 35,000 yards of landfill materials since 1996, according to the hospital's own records.
But Abelkis says that it's not just about well-meaning efforts to help the environment. "Everyone has good intentions," he says, "and good intentions might be part of my motivation, but at the end of the day, when our program can save the hospital $600,000 a year in avoided costs or cost savings, that's not only good intentions, but also good business sense."
Abelkis is at the forefront of a movement that aims to transform the way supply chain organizations think about their potential impact on the business and the business' potential impact on the broader community. This movement offers the possibility of long-term environmental gains for the planet and long-term competitive advantages for enterprises willing to take the lead in introducing a culture of sustainability into the way that supply management operates as a function.
The Movement toward Green
Green supply chain has been getting a lot of attention over the past year, but, as a concept, it's nothing new. Joseph R. Carter and Ram Narasimhan put out a paper on "Environmental Supply Chain Management" through the Center for Advanced Purchasing Studies (CAPS) in 1998 based on a focus study of "environmental issues of relevance to supply chain management." Before even that, the International Green Purchasing Network (IGPN) was founded in Japan in 1996.
Dennis Damman, director of engineering at Schneider National, the Green Bay, Wis.-based transportation and logistics services provider, notes that companies like his have long had an interest in becoming more efficient and running more efficient equipment. But in the 24 years that he has been with Schneider National, he has seen the focus shift from internal operational issues toward more global environmental concerns. "What started out as finding the truck with the best fuel economy has migrated over the last several years to not only fuel economy, but also a focus on emission reduction," Damman says. That has led to changes in how Damman and the engineering team at Schneider National spec the company's tractor equipment, with full aerodynamic effects, fuel efficient tires and lower engine horsepower ranges, for example, with an eye to being more environmentally friendly. The company also uses driver training and incentive programs to reduce idling, resulting in Schneider National currently idling its tractors at less than half the industry average.
Regulatory authorities have driven some of this change, with transportation companies moving to meet emission mandates from the Environmental Protection Agency, non-attainment area restrictions on truck idling in metropolitan areas that have not met air quality standards, and other government regulations. Voluntary programs have promoted the shift, too. For example, the EPA launched the SmartWay program in 2004 "to address the environmental and economic challenges surrounding growth in the freight industry," and the program now encompasses more than 600 businesses interested in improving their bottom lines as well as the environment. The EPA says that its SmartWay partners have saved 600 million gallons of diesel fuel — a cost benefit of almost $2 billion — and eliminated nearly 7 million metric tons of carbon-dioxide emissions that contribute to global warming thanks to three-year commitments to upgrade their trucks. The program also has recognized specific companies for environmental leadership with its annual SmartWay Excellence Awards, which Schneider National, for example, has received for the past two years running.
Public pressure clearly is playing a greater role in pushing companies toward meeting broader social obligations as well. In a recent survey by consulting firm McKinsey & Co. of 391 CEOs at companies around the globe, 95 percent of the respondents acknowledged that society has higher expectations for how companies will meet "public responsibilities" than five years ago, and more than half said that those expectations will rise in the next five years. "Many of the CEOs we interviewed observed that satisfying the shareholders is no longer good enough: consumers will punish companies that don't fulfill their public responsibilities, causing their market shares to decline," write Debby Bielak, Sheila M.J. Bonini and Jeremy M. Oppenheim in an article about the survey for the October 2007 issue of The McKinsey Quarterly.
Building a Culture of Green
This grassroots pressure, in turn, is prompting companies to start looking at the environmental impact of their supply chains and how they can start pushing green upstream to their suppliers. Mega-retailer Wal-Mart, for example, recently announced that it would start measuring the energy used to create products in its supply chain under a partnership with the Carbon Disclosure Project. Schneider National works with its tractor supplier on ways to improve the insulating capabilities of the tractor and to integrate new cab-cooling technologies. These projects will help Schneider National meet its own objectives for reducing the use of air conditioning in its tractors in the summertime. "We work very closely with them as we test components or different products to let them know how we think those products are stacking up, and we provide testing for some of their new products to validate the savings, too," Damman explains.
Yet while the drive toward a greener supply chain appears to be gaining momentum, the companies that are actually making steps in this direction remain in the minority. So while 59 percent of the CEOs in the McKinsey survey said they believed that their companies ought to incorporate environmental, social and governance considerations into how they manage their supply chains, only 27 percent said they currently do so. The primary obstacle, as the CEOs saw it, was the difficulty in changing practices at their companies' suppliers.
But executives working around green supply chain issues suggest that the place to start a green initiative is inside the four walls of the enterprise. One of these executives, Mark Buckley, vice president of environmental affairs at Staples, the Framingham, Mass.-based office products retailer, says that the way to incorporate green into the supply chain is to first integrate green values into the broader culture of a company. Buckley's company has adopted a set of internal business guidelines dubbed Staples Soul, focused on diversity, commitment to the local community, business ethics and the environment. "The whole idea of Staples Soul is that it speaks to the culture of our business," says Buckley, who has been with the company for 17 years, the past five in his current position. "We're trying to embed this idea of sustainability into the way that we operate our business at every level and across every division of the company."
For the company's supply chain executives, this means that as they think about how to increase the efficiency of Staples' distribution centers or delivery operations, they are also thinking about the environmental impact of their decisions as well. "We're trying to find ways to show people where they can make these linkages and actually not only derive real business value but also do the right thing at the same time." This philosophy has led to a host of initiatives at the retailer, including programs as simple as installing skylights in distribution facilities to cut down on lighting requirements during daylight hours, and as complex as incorporating dual-speed drive motors on conveyer systems with localized controls in the facilities to help reduce energy usage. Through these and other initiatives, Staples has reduced its per-square-foot electricity consumption by close to 15 percent across all its real estate since 2001. The company's goals moving forward include reducing, by 2010, its overall carbon impact by 7 percent on an absolute basis compared to a 2001 baseline.
Green Best Practices at BCH
At Boulder Community Hospital, the organization's green initiatives began at the grassroots when a number of the staff who had been taking recyclables from the hospital to a recycling facility on their own formed a "green team" to set up a formalized recycling process within BCH. They found a sponsor in the organization's chief financial officer, and the hospital's administrators and board of directors subsequently adopted an environmental statement of principles and policies that helped enshrine green in BCH's overall culture. The hospital hired Kai Abelkis as its environmental coordinator in 1999 on a part-time basis, with Abelkis working 10 hours a week for BCH in addition to his full-time job with a recycling company. After two years of working to improve the hospital's recycling program and winning a couple of awards for his work at BCH, Abelkis saw opportunities to expand his work at the organization and was able to convince the hospital's leadership to bring him on full-time.
Abelkis also focuses on culture as a key enabler for the success of green initiatives, specifically on the importance of creating an organizational culture that enables individuals to pursue projects that have bottom-line as well as environmental benefits. "We've empowered people to look at efficiencies and ways to improve upon their departments with the environment in mind," he says. As an example, Abelkis points to George Dempster. When Dempster was the sterile processing director with BCH (he's since left the organization), he realized that about 20 percent of the hospital's waste was so-called "blue wrap," a polypropylene material used to protect patient gowns and toiletries, medical devices and surgical instruments from contamination. Dempster requested and received $120,000 from the hospital's management council to purchase reusable hard containers to replace blue wrap where possible. Within two years, the initiative not only had reduced a significant portion of the waste generated at the hospital's facilities but had also earned back the initial investment and saved the hospital more than $180,000 in blue wrap costs.
BCH also has taken its initiatives upstream, working with its suppliers on environmental projects where possible. Dempster, for instance, convinced Stryker to use custom-made containers for one product that the hospital purchased from the medical devices company, again helping the hospital reduce its blue wrap wastes and costs. Further, Abelkis has promoted green procurement through his work with Novation, an Irving, Texas-based healthcare contracting services company that acts as a group purchasing organization for member hospitals. Abelkis serves on the integrated nursing council at Novation, which in 2007 won the Champions for Change award for the fourth consecutive year from Hospitals for a Healthy Environment (H2E). Novation, which accounted for $31.6 billion in purchases in 2006, works on initiatives that include safer food alternatives, management of pharmaceutical waste, reduction-reuse-recycle initiatives and chemicals management policy on behalf of its members.
In fact, Abelkis envisions a broader role for the GPOs in promoting green procurement by leveraging the members' shared spend in the same way that a channel master like Wal-Mart is able to wield its own massive buying power. Increased GPO involvement in green initiatives could help to drive greater participation across the healthcare industry, which Abelkis sees as key to the long-term success of the green supply chain in his industry. "What's going to sustain this initiative is having the entire industry adopt these principles," he says. "Sustainability has to become part of our decision-making process."