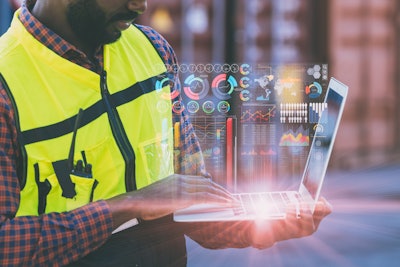
Picture a warehouse where AI-driven insights guide operations in real time, preventing costly damage and reducing safety incidents while predictive maintenance flags critical repairs before machines fail. These aren’t lofty predictions; they’re real, proven use cases happening today in industrial settings.
With supply chain disruptions costing businesses an average of $45 million annually and up to $182 million in high-risk sectors, manufacturers are under pressure to optimize every aspect of their operations. Here’s how Industrial Internet of Things (IIoT) solutions are helping businesses reduce downtime, streamline supply chains and enhance worker safety.
By integrating smart sensors, AI-driven workflows and data-powered automation, companies are not just staying competitive; they’re building resilience in an increasingly challenging market.
These costs highlight a key challenge in modern supply chain management. The push for operational efficiency often comes at the expense of stability. Disruption-free operations depend on multiple factors, yet one that is often overlooked is having a robust safety infrastructure within your warehouse or manufacturing facilities.
An inadequate safety infrastructure increases the risk of unplanned downtime, whether through accidents, equipment damage or inefficient workflows. These disruptions create ripple effects throughout the supply chain, delaying orders and driving up costs. Safety-related disruptions are a consequence of deploying traditional safety methods that were not built for the scale and speed of today’s warehousing facilities, leaving operations exposed to avoidable setbacks. Reducing this level of risk requires a new approach to safety.
The limitation of reactive risk management
Traditional safety infrastructures rest on an outdated premise: that protection is fundamentally reactive. Take safety barriers, for example, whose only purpose used to be providing physical protection until they became too damaged to remain in use. This approach creates three critical vulnerabilities in modern high-velocity operations.
First, damage assessment still relies on manual inspections, which fail to detect structural weaknesses beneath the surface. Parts are either replaced while still functional which wastes resources, or if left too long, can lead to sudden failures and costly repairs. Maintenance costs come at the most unexpected times and can cause strains on budgets and serious knock-on effects with cash flow.
This reactive approach might have sufficed in earlier operational environments, but it creates substantial business risk in today's high-throughput facilities where even minor downtime translates to significant revenue impact. The emergence of smart technology is addressing this challenge, transitioning from passive protection to active, real-time intelligence.
The shift to AI-powered safety
The integration of IIoT sensors and AI into physical protection systems creates a continuous awareness network throughout the facility. AI processes data from sensing nodes embedded in safety barriers, not only detecting and communicating impact events in real-time but also analyzing patterns to predict potential risks. This transforms previously static protection into a system that adapts and responds intelligently to evolving conditions.
This shift eliminates the inspection gap by providing continuous structural assessment of protection elements. AI enhances traditional monitoring by assessing impact severity, detecting anomalies and forecasting potential failures. Rather than relying solely on scheduled inspections, operations managers receive immediate notifications of impact events, along with AI-generated insights into structural integrity. Staff are then able to intervene proactively and plan ahead before minor issues escalate into operational and financial disruptions.
More significantly, this approach transforms safety data into actionable operational insight. AI analyses impact patterns across the facility, identifying workflow friction points and inefficiencies that static barriers could never reveal. By uncovering these trends, businesses can transition from reactive safety measures to data-driven, predictive strategies that contribute to reducing downtime and boosting efficiency.
The strategic value proposition
The economic case for investing in a smart safety infrastructure extends far beyond risk reduction. OpenText's supply chain survey found digitally optimized supply chains can reduce procurement costs by 20%, decrease overall supply chain costs by 50% and increase revenue by 10%. Yet, 72% of suppliers experiencing disruptions lacked the visibility necessary to implement rapid, effective solutions.
This lack of real-time visibility is why many businesses struggle to reduce supply chain disruptions. The report by Interos indicated that 90% of organizations lack awareness of sub-tier supplier disruptions for up to 48 hours, leaving them vulnerable to customer dissatisfaction, brand damage and substantial losses. Intelligent safety systems bridge this gap by turning safety systems into active data sources, instantaneously giving operations managers a clearer picture of risks and incidents. This high level of awareness enables continuous optimization of warehouse layouts, workflow design, and resource allocation based on real-world performance data rather than theoretical models and periodic reviews.
What is most compelling is how intelligent safety infrastructure transforms capital planning. Traditional facilities management treats safety infrastructure as a depreciating asset with predictable replacement cycles. In contrast, smart systems appreciate in value as they accumulate data. Each impact event enriches the system's predictive capability, allowing increasingly precise resource allocation. This inversion of the traditional depreciation model fundamentally changes how organizations approach capital expenditure decisions, treating safety technology as an appreciating asset rather than a consumable expense.
Smart risk-reduction systems also change how employees interact with safety itself. When staff see that safety measures adapt to real-world conditions and contribute to their productivity and safety, compliance shifts from a rule-based obligation to a shared investment in efficiency and protection. This perceptual shift boosts a company’s safety culture and generates employee-led innovation in workflow design, productivity and job satisfaction.
Safety as competitive differentiation
The smart warehouse will differentiate itself not through automation alone but through the elimination of operational friction. Intelligent safety infrastructure provides the foundation for this transformation by creating an environment where protection and productivity operate as complementary forces rather than competing priorities.
Companies that are reluctant to invest in modern safety solutions such as traditional steel barriers face an increasing competitive disadvantage compared to those that do. Clinging to steel safety barriers in a modern warehouse is like relying on paper maps in a GPS-driven world. New materials such as polymer do not just dissipate impact energy better and maintain their structural integrity, but they can provide IIoT-powered data that is used to make operations more efficient.
Forward-thinking companies see safety as a strategic investment rather than a compliance cost. An intelligent safety system substantially decreases the risk of downtime, protects assets and helps keep operations running smoothly, strengthening customer satisfaction and profitability. Businesses that adopt this strategic position will be the ones setting the standard for resilience, efficiency and industry leadership.