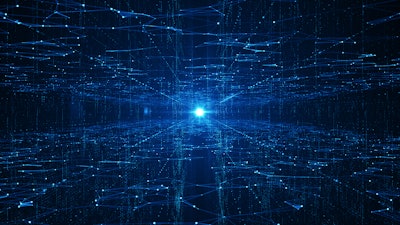
In the backdrop of today’s heavily globalized economy, the global supply chain landscape has never been more complex or fraught with challenges, particularly in the context of geo-political, environmental, and regulatory risk. As international trade has become increasingly interconnected, companies have been forced to navigate a complex web of evolving regulations and compliance requirements across multiple jurisdictions. The heightened focus on sustainability, human rights and national security has added in new layers of complexity, pushing organizations to rethink supply chain risk management and resilience from the ground up.
Recent legislation such as the EU’s Corporate Sustainability Due Diligence Directive (CSDDD), and the U.S.’s historic Uyghur Forced Labor Prevention Act (UFLPA), has placed unprecedented pressure on companies to maintain comprehensive visibility into their supply chains. The risk of failing to take action is significant, as demonstrated by the number of shipments detained by the CBP through the enforcement of the UFLPA since 2022. Companies are no longer only responsible for conducting due diligence on their direct, Tier 1 suppliers – but are also being held accountable for ensuring compliance across their entire sub-tier supply chain, extending all the way up to raw material providers.
In this environment, companies need to be more aware than ever before of where and how their products are made. Effective supply chain risk management has become not only a strategic advantage, but a critical necessity and companies must adapt their approach to anticipating and mitigating regulatory risks, in an effort to maintain operational resilience, safeguard their reputations and ensure long-term growth.
Where to Begin?
According to McKinsey, an auto manufacturer has around 250 tier-one suppliers on average, going up to approximately 18,000 suppliers across the full value chain. With nearly every supplier having several suppliers of their own, the map of supplier relationships can get exponentially big, exponentially fast. This can be incredibly overwhelming for compliance and procurement teams tasked with identifying and mitigating end-to-end supply chain risk. They find themselves asking where to even begin.
Typically, the process begins with supply chain mapping. Identifying and mapping suppliers up to the raw material input level is a prerequisite for comprehensively identifying and managing sub-tier risk. However, achieving comprehensive n-tier visibility is one of the biggest challenges facing supply chain organizations across the board. According to a Deloitte CPO study, only 15% of Chief Procurement Officers have visibility beyond their tier-one suppliers.
Historically, supply chain mapping has been a resource-intensive and time-consuming process. Companies reach out to their direct (Tier 1) suppliers for information about their Tier 2 suppliers and then cascade that outreach further upstream until they reach the end of the supply chain, typically the raw material producers. Over the last decade, we’ve seen the emergence of supply chain mapping software technologies that have streamlined a part of this process by moving data collection away from emails and spreadsheets and towards online logic-based questionnaires.
Although this has significantly decreased the burden of maintaining and reconciling information received from multiple suppliers from disparate data sources, the approach is still very resource intensive as it relies on repeated supplier outreach, plus validation and verification of supplier responses. It can therefore take several weeks, if not months to map out product-specific supply chains, let alone begin the risk screening and adjudication process. Furthermore, supplier response rates can start to wane as we go further upstream, typically dropping off at Tier 3 or Tier 4, leading to gaps in visibility at the raw material level.
The Potential for Automation
So, what are the alternatives to questionnaire-based, inside-out supply chain mapping? How might companies gain insights more quickly, maximize internal resourcing, and reduce survey fatigue across suppliers?
The most obvious answer is through automation – and one of the ways in which supply chain mapping technology providers are approaching this is by automatically mapping supply chains using publicly available shipment data. Software providers that can harmonize, resolve and draw relationships between suppliers and buyers derived from billions of publicly available shipment records, can effectively enable companies to identify upstream supplier networks within minutes via a powerful knowledge graph, entity resolution engine, and accessible UI. Automatically mapping and identifying upstream suppliers can, in turn, enable compliance and sourcing teams to batch screen sub-tier suppliers for potential risk, limiting outreach and follow-up only to high-priority cases where additional information is required for risk adjudication, and significantly reducing costs. Instead of waiting months to start making decisions on supply chain risk, companies can start that process almost immediately.
How to Get the Most Out of AI
Many supply chain mapping and risk management software providers have also embraced the emergence of artificial intelligence and large language models (LLMs) as a potential solution. While AI holds immense potential for enhancing supply chain visibility, it’s essential to use it thoughtfully and judiciously.
One of the ways in which AI is increasingly being leveraged for supply chain mapping is in terms of generating “predictive” supply chains. Software companies are using generative AI to predict, with an associated level of confidence, the upstream supply chains for a given company and/or product based on a known set of inputs. Although this data can certainly be beneficial from a risk modeling perspective, it should not be used as an alternative or proxy for mapping a real supply chain, and identifying real risk. Particularly in the context of compliance, in which regulatory requirements drive risk assessment, it's absolutely crucial to base risk-decisioning on real, actionable data with clear data provenance.
Another way in which AI can be used to build workflow efficiencies is through synthesis and validation of real-world supply chain data. Companies can use LLMs to validate recurring patterns identified in large volumes of shipment data and use the results to filter out non-relevant risks and/or illogical relationships. For example, LLMs can be used as a first-level check to determine whether a specific component, say polysilicon, is used in the production of another downstream component, silicon ingots, which in turn may be used to produce silicon wafers that are ultimately used in the production of semiconductors. In doing so, supply chain mapping technologies can automatically filter out data (in this case, input components) that are not relevant to a company’s product or business line, effectively reducing noise, and ultimately enhancing and accelerating supply chain mapping and risk identification workflows.
It’s important to acknowledge that although AI can create efficiencies, there's a trade-off between speed and accuracy that must be carefully managed. It’s worth mentioning that the models mentioned above are most effective when they are designed using human-in-the-loop approaches that ensure high levels of accuracy. The key to effective supply chain visibility lies in striking a balance between leveraging advanced technologies and maintaining a foundation of reliable, high-quality data. AI and advanced analytics should be used primarily for synthesis and validation to enable workflow efficiency gains, drawing clear distinctions between relevant, data-driven risks and potential risks generated through predictive modeling. For operational aspects of supply chain management, such as modeling goods movement and optimizing logistics, generative AI can play a prominent role. However, when it comes to compliance and legal considerations, the focus should remain on real, current data and verifiable risk.
As supply chain mapping becomes increasingly crucial in today's complex global economy, companies must adopt a nuanced, data-driven approach to risk management. By focusing on achieving sub-tier visibility and leveraging the power of public data and carefully applied AI, organizations can navigate the evolving regulatory landscape while building more resilient and transparent supply chains. The future of supply chain risk management lies in the thoughtful integration of technology with high-quality, verifiable data, to drive informed decision-making, and ensure compliance in an ever-changing global marketplace.