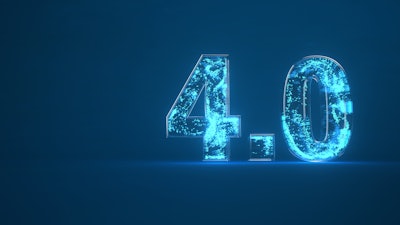
Today’s warehouse and distribution operation is as much a source of data as it is a source of the products being sold, shipped and delivered. Data from equipment, workers and the facility infrastructure itself can tell us who and what is performing to expectation; how much energy is consumed; how much effort or time is being devoted to a given operation; or even where a specific lift truck or worker is located at any given moment for potential dynamic routing adjustments. But the principles of Industry 4.0 compel us to ask: What then? How do we connect this range of data to larger trends? How can we use the data to help identify not just the inefficiency itself but also the root cause of and, ideally, the optimum resolution for that inefficiency?
Putting It All Together
When we can analyze and understand our operation to a greater degree, we can use the data — data that we’ve spent money, effort and time to collect — to its fullest potential. How?
Consider a fleet management system that collects and reports maintenance and repair data. The data may tell us, for example, that a particular lift truck needs its tires replaced more frequently than other lift trucks in the fleet. But do we know why the tires are wearing faster? Do we know what conditions the lift truck is operated in, what the experience level of the operator is, or if daily checklists are being performed? Without the “why,” all we really know is that the tires are wearing out.
But when we consider the data as a starting point and not the end goal, the potential of Industry 4.0 comes into clearer focus and the data becomes what it was always meant to be — a tool that can lead us to outcomes such as:
- Improved Equipment Utilization — Take our previous example of tire replacement. Following Industry 4.0 data aggregation principles, using the breadth of data we collected, we not only can see that these tires need frequent replacement but also can more accurately identify the root cause. We might combine maintenance data with tracking data from our Real-Time Location System and telematics operator tracking to see that the route this particular operator follows is contributing to tire wear. Using this information, we can take any of several possible actions, such as implementing a more targeted maintenance strategy for lift trucks in this route, creating a “no-go” zone in our warehouse management system or providing the operator with additional lift truck operation training when navigating this route.
- Improved Operational Efficiency — We also can use collected data to refine processes and optimize resource allocation. Consider lift truck charging, for example. Energy monitoring data can tell us not only if and when a lift truck is charged but also if we’re making the most of our opportunity-charging times. We can see exactly when an operator is on a break or at lunch, if the lift truck has been plugged in to the charger during those times or when a shift ends. This ensures equipment is ready for use by the next shift and avoids unnecessary downtime.
- Improved Cost-efficiency — Understanding “why” something is happening empowers us to make better, more-informed decisions that can contribute to lower operating costs. Are common congestion areas slowing down your automated trucks? Using data collected from the lift trucks themselves during normal operation can allow us to optimize facility layouts or route scheduling to improve material and traffic flow, improve overall efficiency and, ultimately, maximize our ROI on equipment.
Whether it’s reducing maintenance expenses, improving energy management or optimizing labor and automation resources, data-driven insights will almost inevitably lead to a leaner and more efficient operation.
Predicting the Future With AI
Imagine the ability to identify a variable, such as lift truck routing or packing location; modify that variable; and see how that modification could affect overall efficiency and profitability. Predictive analytics based in artificial intelligence (AI) and simulation when trained with existing data can help us determine if we can add more SKUs with existing resources, if we need to hire more workers or purchase more equipment or if we should consider facility expansion options.
AI assisted predictive maintenance can be another game-changer. Instead of replacing parts on a simple set schedule or according to basic usage hours, we can begin to apply AI to bring in other maintenance-influencing factors like environment, current operating status of the mechanism itself and even forecast duty cycles in the coming days to better predict specific maintenance needs. Additionally, AI assisted predictive maintenance can further help ensure a technician services major components of the lift truck only when there’s a need. This approach also can lead to labor savings, as technicians do not need to inspect the lift truck for wear as often.
The First Steps
The journey to Industry 4.0 might seem daunting, but if you’re collecting operational data through telematics, you’re already well on your way to building a foundation that can support future analytics needs. As you dive deeper, your IT department should be engaged at every step — not only to protect sensitive information and systems through contemporary cybersecurity but also to ensure the various systems can communicate with each other within the Internet of Things. Lastly, collaboration with a trusted supplier can streamline data collection and analysis processes, making the transition to Industry 4.0 smoother and more effective.