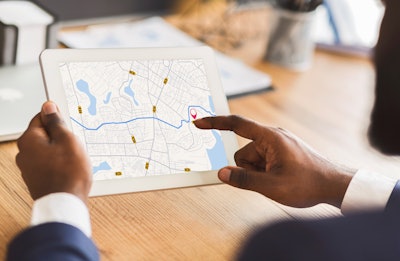
Being able to run business operations as efficiently as possible is one of the cornerstones of every successful enterprise. Greater efficiency means greater productivity which translates into higher profits. But in the complex world of manufacturing, with all its machines, people, and processes that must work perfectly in sync with each other, achieving maximum efficiency can be quite the challenge.
To overcome this challenge, many businesses have begun implementing a variety of location tracking technologies. These technologies come in many different forms and can be used to track both assets and employees in a workplace. Greater control over your assets and staff can allow manufacturers to dramatically improve their workflows, increase overall efficiency and reduce operational costs.
This breakdown will look at the different types of location tracking technologies and how they can be used to increase productivity in a manufacturing plant.
What is location tracking?
Location tracking is a bit of a broad term that can refer to any advanced computing technology that locates, tracks, and records the movement of people or assets. Most of them use some combination of a sender and receiver device, which allows organizations to track an asset’s location in real-time and pinpoint it on a digital map.
Tracking technologies come in a wide range of forms and determining the best one for your business isn’t always easy. Some tracking systems only work outdoors, others only work indoors. Some have very high accuracy or latency while others don’t. Simply put, there is no one-size-fits-all approach. Choosing the right one will depend on what your needs and goals are and the type of environment you’ll be working in.
Below, are the four most common types of tracking technologies you will find on the market. Each one has its pros and cons, so business managers are advised to take time to understand each type and whether they might be a good fit for their business.
1. GPS
A highly common method for location tracking, GPS devices can be attached to an asset that sends out satellite signals which are then processed by a receiver. GPS is especially useful for in-transit tracking due to its long range and low power consumption. However, downsides to GPS include the high cost of tracking devices, and its inability to track assets in indoor locations. The relatively weak strength of GPS signals also limits their accuracy to about 5 to 10 meters.
2. Bluetooth Low Energy (BLE)
Bluetooth Low Energy (BLE) is a short-range wireless technology that uses Bluetooth-enabled tags, which can be affixed to an asset or carried by an employee. These tags give off a signal that is picked up by the receiver—sometimes referred to as an anchor—that acts as a GPS satellite. BLE accuracy depends on the number of receivers in use, with a high number allowing for accuracy of around one to two meters. Benefits of BLE trackers include their high accuracy, low power consumption, ease of use, and their ability to work indoors. Downsides include their short range and inability to work effectively in an outdoor environment.
3. Ultra-Wideband (UWB)
A close competitor of BLE systems, UWB is based on radio technology that uses low power consumption to achieve high bandwidth connections that allow for pinpoint accuracy. It does this through two key signals, Time of Flight (ToF) and Time Difference of Arrival (TDoA) that combine algorithmically to provide an asset’s exact location. Compared to BLE, UWB is a far more accurate and reliable system. However, one significant downside to UWB is the high cost of system installation, which requires a high number of antennas and wiring to be run through the entire facility.
4. Passive RFID
Passive radio-frequency identification (RFID) uses electromagnetic fields to identify and track tags. Because they are powered wirelessly through receivers, they don’t require batteries, making them highly cost-effective. However, they have a very short range, usually only about 15 centimeters, making them more suited for use at checkpoints rather than in-the-field locating. While RFID signals can penetrate cloth and plastic, they cannot penetrate metal.
How location tracking can improve manufacturing efficiency
Depending on a company’s needs, managers may choose to go with one type of tracking system or use a combination of different types. Either way, a well-implemented tracking system should be able to provide the following benefits.
1. Asset tracking
By attaching location trackers to each of a company’s assets, managers can ensure a far more efficient and productive work environment. Knowing both the location and quantity of stored materials can prevent unexpected shortages or pile-ups that needlessly disrupt the production line. Any perishable goods can be tracked to ensure they are used on a first-in, first-out basis, thus reducing waste. Tracking your equipment also means that staff will spend less time searching for a misplaced item, allowing them to focus on their core tasks.
2. Increased efficiency and space planning
In a high-traffic environment, it can often be difficult to monitor how long it takes for a product to travel through the production line. By tracking each product, managers can determine how much time is spent at each stage of the manufacturing process, allowing for bottlenecks to be identified and rectified. Having a better sense of how your products are transported through the facility can also provide insights on how to improve the layout of your workplace. An optimized layout that shortens travel distances and increases organization can dramatically boost efficiency.
3. Better health and safety
Tracking all your heavy equipment can have immediate benefits for health and safety by reducing the risk of accidents. For instance, forklifts can be tracked to ensure they are being used correctly and safely. For high-risk areas, access monitoring allows managers to restrict unskilled workers from wandering into areas they are not qualified to be in. Knowing the location of all your staff also makes it easier to perform a headcount in an emergency evacuation. If any staff are unaccounted for, their tracking tags will tell you exactly where they are. With improved safety protocols comes fewer accidents which translate into lower insurance premiums.
4. Improved quality control
The quality control process is a vital step in manufacturing, both for regulatory compliance and ensuring that no faulty products reach the customer. Implementing an automated tracking and data recording system can remove the risk of mistakes due to human error. Tracking data on equipment use can also highlight when routine maintenance needs to be carried out, ensuring that periods of downtime are kept to an absolute minimum.
5. More efficient shipping and delivery
For manufacturers that deal with high-value goods, shipping errors can be highly frustrating, costly, and time-consuming to correct. By tracking all your products as they are loaded onto vehicles for transit, you can ensure all required items are on board before departure. Furthermore, this data can be used to narrow down where mistakes or even theft are happening in the shipping process.
Final thoughts
In the past few years, the number of businesses using some form of location tracking technology has skyrocketed. More and more managers are beginning to realize just how effective these technologies can be at increasing their efficiency and productivity. It’s even being used in businesses as diverse as logistics, retail, construction, and healthcare.
For manufacturing managers, the ability of location tracking to provide a high level of control over their business operations, combined with its cost-effectiveness and high scalability, makes it a required technology for the modern age.