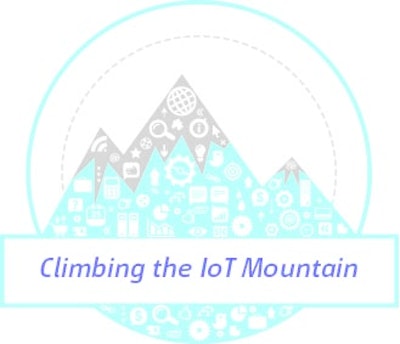
Adding the Internet of Things (IoT) to the manufacturing process is a lot like standing at the foot of Mount Everest, ready to climb the world’s tallest mountain. You know you want to get to the top but you aren’t really sure how you will get there or what obstacles you’ll encounter along the way.
The world of manufacturing is at the start of its IoT ascent. Though author, David Turbide, reports in “Manufacturing Embraces the Industrial Internet of Things,” that the IoT, also known in manufacturing as the Industrial Internet of Things (IIoT), is a “logical extension of automation and connectivity that has been part of the plant environment for decades, primarily in the area known as machine-to-machine (M2M) communication,” there is still much to learn.
In fact, despite this history, Turbide himself warns in his article that “the transition from M2M to full IIoT presents interesting challenges that manufacturers must address before the technology gets out of hand and threatens rather than enhances the benefits it promises to provide.”
That’s the bad news. The good news is manufacturers do not have to implement IoT all at once. They can take small steps to get to the top—a place where they’re capturing all information from the shop floor and along the supply chain in real time then turning that data into actionable insights.
Also good is the fact that there are already some successful manufacturing pioneers who have paved the IoT highway for others to follow. General Electric Co., for example, employs 10,000+ sensors to measure temperature, humidity, air pressure and production machine data in real time at its Durathon battery plants. The company uses the data it collects to monitor production and adjust processes in real time, and to trace battery performance back to specific batches and steps in the manufacturing process.
Connected Manufacturing
IDC Research Inc. reports in its white paper, “IoT and Digital Transformation: A Tale of Four Industries,” that where IoT is employed in manufacturing—to connected supply chains, assets or products—will vary by manufacturer. The white paper states that companies that own their own facilities are likely to be early adopters of IoT in the plant, while those making products with longer life cycles may use IoT to change their products and services.
The important thing to note, according to the IDC white paper, is that IoT is making its way into products and processes. By leveraging IoT to create connected products, companies can now offer IoT-enabled services to their customers. Likewise, they can employ IoT on the shop floor to increase efficiency and effectiveness in their manufacturing operations. “The benefits are many—increased capacity on production lines, easier product customization, and tighter links between supply and demand,” the white paper states.
With IoT in the mix, companies can engage in on-demand manufacturing at a higher level than ever before, states Kevin Lyons, associate professor in the Department of Supply Chain Management/Supply Chain Archeology Lab at Rutgers Business School. “In the past, manufacturers just produced as much product as they possibly could, and if they didn’t sell everything, then they had a piled up inventory. Obviously that’s a big expense. With IoT’s predictive analytics capabilities, you can pinpoint what production is needed, where and how much, in real time.”
He adds that with the right amount of IoT in place, and a streamlined supply chain, companies can trim costs from the manufacturing process, reinvest that money into additional technological advances, which in turn will save money on the labor side.
Dr. Achim Kruger, vice president of Operational Excellence Solutions at SAP, agrees, stressing that with the IoT, there is “a lot more information available from products or assets that can help manufacturers make optimal decisions. IoT is really about combining data from the business, and from the shop floor, to make better business decisions.”
Ask the Right Questions
But with all these advantages where is IoT really at in manufacturing? PricewaterhouseCoopers (PwC) states in, “Building an Internet of Things Manufacturing Ecosystem,” that one in three manufacturers report using data-driven technology in the manufacturing plant only, while one in four deploys it in both the plant and the warehouse.
Taking that a step further, PwC’s report points out that “despite the overall growth of smart sensor deployment, only one-third of U.S. manufacturers are currently leveraging it, while one-quarter indicate plans to adopt the technology. Many manufacturers are just beginning to deploy devices to gain greater situational awareness of operations, but PwC notes that 24 percent of manufacturers have no plans to implement IoT technology and another 24 percent report they plan to do so during an unspecified timeline.
Bobby Bono, an audit partner with PwC, recommends companies ask a handful of key questions to determine their IoT goals, then strategically implement the technology over time. Consider the following questions to help craft an IoT strategy:
- Have you conceived an IoT ecosystem strategy?
- Are you considering IP-enabled products that can lead to after-sale services?
- Does your talent base need retraining to build an IoT strategy?
- Have you identified what and where data can be collected?
- Are you squeezing enough meaning out of the data you collect?
- Are employees using the data optimally?
Implement in Stages
Before adding IoT anywhere in manufacturing, Bono recommends companies carefully consider they types of data they need and why, then look at how they will apply captured data to their operations.
“It’s not a one size fits all,” he stresses. “Every company will have different data needs.” One company, for example, may seek to reduce its energy costs, while another wants to identify what is leading to a larger than acceptable number of product returns. And different goals will lead to different IoT strategies.
David Stephenson, owner of Stephenson Strategies, a strategic consulting firm concentrating on services pertaining to IoT implementation, believes the assembly line is a good place to begin implementing IoT. These sensors can provide information about equipment performance, product design and usage patterns to improve processes.
As sensors begin gathering data, companies cannot overlook the need to invest cloud storage to house the volumes of data they collect and advanced analytical tools. “They will need tools that allow them to do real-time data analysis, which will help with all sorts of operational changes,” Bono says.
Putting IoT Data to Use
The benefits of IoT really add up once sensors are in place.
Putting sensors on capital equipment might provide advance warning of potential problems with the equipment, so that workers can perform predictive maintenance rather than rely on scheduled maintenance, which Stephenson says can be “somewhat of a crap shoot.” It may also allow companies to increase the time between maintenance intervals because the gathered data will more accurately show when these things need to be done. Maintenance improvements like these can reduce production downtime due to equipment failures.
“These devices can predict when machines are going to break down, so you can fix them before they break,” says Gil Perez, vice president of digital assets and IoT at SAP.
In addition, putting sensors on production equipment may also improve operating efficiency because companies can do M2M coordination of pieces on the assembly line so that a change in the condition of Component No. 1 will trigger a change in the operation of Component No. 2 and so on down the line. “It really can improve day-to-day efficiency,” Stephenson says. “I refer to this as precision manufacturing, and IoT will allow manufacturers to do that to an extent that was never possible before.”
A key advantage of IoT is getting real-time feedback on manufacturing processes, which can allow companies to adjust processes for greater efficiencies. Take energy usage for example. Sensors can identify the greatest consumers of energy in the manufacturing process. “Manufacturers can then ask themselves if there is a way to be more efficient,” Bono says. “Maybe they can do those things at different times of the day, when energy costs are lower. Or maybe there is an alternative process that would use less energy. IoT is about gathering real-time information about your processes that allow you to make real-time adjustments based on actual data.”
Data from IoT sensors can also help companies make sound decisions about their supply chains. For example, it might help them determine if it makes sense to source a subcomponent or make it themselves. “Maybe you realize that it’s more efficient to make some subcomponents,” he says. “Or maybe you realize the subcomponent you currently make consumes too much energy during the manufacturing process, and it’s actually cheaper to outsource it. With IoT, you can adjust your supply chain but you will be using hard data to make those decisions.”
Perez takes the use of IoT in manufacturing a step further and predicts a day when IoT and Big Data merges with 3D printing. “Companies can use this data to determine which parts they want now, which ones make sense to digitize and 3D print, and where it will be most financially feasible,” he says.
SAP Releases New Solution to Help Manufacturers Benefit from IoT
SAP SE recently introduced the SAP Asset Intelligence Network and the SAP Predictive Maintenance and Service Solution to help equipment manufacturers, service providers and asset operators benefit from the Internet of Things as the proliferation of sensors and smart devices transforms asset management.
The SAP Asset Intelligence Network offers a single global register of model and equipment information in a secure cloud platform. This connects multiple business partners for inter- and intra-company collaboration. This new network permits SAP S/4HANA to facilitate business-to-business integration for asset data. The network provides a common collaboration platform for asset-related information as well as the business context for predictive maintenance and service. Advanced analytics for identifying and understanding trends can be shared across the network and it is possible to notify both manufacturers and operators about imminent shortfalls or failures.
The SAP Predictive Maintenance and Service Solution, meanwhile, is designed to help businesses decrease maintenance and service costs, while boosting the availability and reliability of enterprise assets. By using predictive analytics on the SAP HANA platform, the solution processes vast amounts of real-time operational data from sensors and smart assets.
This solution provides built-in capabilities that analyze sensor data and monitor equipment behavior remotely for businesses in asset-intensive industries as well as original equipment manufacturers, offering new service business models for customers. The solution provides predictive models for machine learning and closed-loop integration with business systems to trigger corrective actions in service and maintenance systems to avoid unplanned downtimes.
“These tools allow users to leverage data from the real world and make better decisions on when to maintain or service assets,” says Dr. Achim Kruger, vice president of Operational Excellence Solutions at SAP.
IoT by the Numbers
1/3 - Of U.S. manufacturers report that they currently use IoT.
24 percent - State they plan to implement IoT technology over an unspecified timeline.
24 percent - Report having no plans to implement IoT technology.