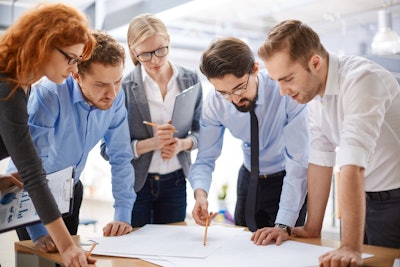
The manufacturing industry is complex—to say the least—thanks to thousands of moving parts and a wide spectrum of issues to address on a regular basis. A big challenge for most manufacturers is managing a global perspective on regulations, sourcing and outsourcing, and competition. The 2009 recession increased hardships for organizations, forcing many executives to review their existing processes and discover ways to both increase productivity and reduce cost.
This opened the door for manufacturers to implement a variety of changes throughout their organizations. However, a 2014 PMI study1 indicated that 82 percent of companies do not consider themselves to be highly-effective at managing change. They also found that nearly 15 percent of every dollar spent on strategic initiatives is lost due to poor project performance. These results can be directly traced back to insufficient communications and a lack of leadership.
To implement effective change management programs, organizations need a structured process that will coordinate people, systems and technology so that workflows are controlled and performed differently. Sustaining lasting change requires management and employees alike to comply with the change requirements and successfully meet company objectives.
Getting Started
Teams: The first step is assembling a team of employees from all levels of the company. One critical factor to successful change management is having an executive sponsor who engages employees across the enterprise, eliminating bottlenecks in the process. Managers of specific teams affected by the change should also be involved to identify critical needs and enforce the change management with direct reports. The most successful projects include employees from all different levels of the organization, which enables the team to examine and take into account a variety of viewpoints. Plus, employees typically feel more empowered when they contributed to the change.
Areas of change: The next step is to identify areas and processes in need of improvement. Start by looking at the five-year plan to determine if any changes are needed before the deadline approaches. The five-year plan also will determine what resources, facilities, equipment, suppliers and contract vendors are needed. Identify weaknesses with a supplier early on and determine if an improvement in the quality process can be made at their site.
This can be traced back to company objectives as well. For example, one company was trying to reduce the backorders and late customer deliveries. The initial thought was that production was to blame for the delays, but after further investigation they found that the root cause was actually the receiving process at the warehouse. By automating this process and prioritizing incoming material, the company was able to reduce production delays by over 42 percent and backorders by 46 percent.
Buy-in at all levels: Since most employees outside of the C-suite are not too concerned with financial ROI, managers need to show them how the new process and procedures will benefit them with greater efficiency and no added complexity. For example, when rolling out a new workflow system, piloting the system for one process shows users across the organization how the process is simplified and the benefit of other tools, such as analytics dashboards, to view issues and trends earlier in the process. Select an IT system that is easy-to-use, otherwise users will avoid it and return to manual processes.
Measuring success: Now you need to identify milestones and metrics around each change to track progress and success of the program. If you can’t measure it, you can’t manage it. Building out key performance indicators (KPIs) and tracking them at different intervals provides enterprises with measures of success for the team and a chance to make modifications before they get too far down the project path. Analytics tools are helpful here because they provide the overview that enables management to identify issues and trends earlier and in-turn make necessary adjustments to resolve the concerns before they affect the bottom line.
Implementing change within an organization is difficult. If the new process or software is too difficult to use, employees will avoid processing changes in the system which could result in product or compliance issues. That’s why it’s imperative that change management extend throughout the organization, from the boardroom to the shop floor.
(1 – Enabling Organizational Change through Strategic Initiatives, Project management Institute (PMI), March 2014)