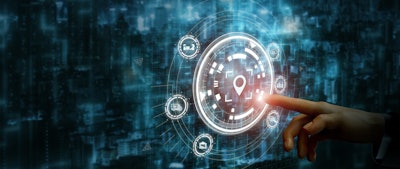
There are few industries that remain untouched by the tsunami wave of automation, machine learning, and artificial intelligence (AI) innovations. These advances are spectacular, as automating important yet routine processes leads to increased productivity, reduced errors, and frees up employees to focus on higher-value tasks. The efficiency boost allows for cost savings and scalability at levels that would have been hard to imagine just a decade ago. However, as with all good things, it can be easy to veer off track. This is exactly why “just right” automation is the key to success, particularly in the manufacturing industry.
"Just right" automation happens when the optimal balance between human involvement and automated systems is identified and achieved. It's about strategically automating specific tasks and processes to improve efficiency, productivity, and quality, while still leveraging the valuable and unique skillsets and capabilities of human workers. As Goldilocks would explain it, the porridge isn’t too hot or too cold, it’s just right. As I will explain in further detail, the manufacturing process must not be over-automated or under-automated, the ideal balance must be achieved.
Over-automation
Automation is exciting. It’s a new frontier! But it is absolutely critical not to over-automate. Just because you can automate something, does not mean that you should. Over-automation can lead to negative consequences like unnecessarily taking jobs from valuable and capable employees, underutilizing human skills like problem solving and creative thinking, and even setting your organization up for catastrophe with a lack of human oversight to catch issues a computer could miss. For instance, advising business owners to engage in illegal activities or directing fleeing evacuees into wildfires rather than away from them, because, unsurprisingly, the routes through a fire have less traffic – a human knows why that matters, but in this case automated GPS software did not.
Under-automation
Those cautionary examples may have you questioning if leaning into automation could hurt your company but let me remind you there are also consequences to under-automating. Under-automation in the manufacturing industry can be costly and even life-threatening. If you’re under-utilizing automation in the areas it can truly be impactful, like repetitive, physically demanding, or hazardous tasks, you are doing a disservice to your company, your employees, and your customers. Manufacturers are deeply affected by supply chain disruptions and inefficiencies, with the industry suffering an annual $1.6 trillion injury of missed revenue and companies facing difficult-to-calculate reputational damage due to supply chain issues.
When it comes to companies that provide crucial medical equipment and supplies to patients nationwide, human lives are also on the line. With stakes so high, manufacturers can’t afford to under-automate elements of their supply chain. Relying on an increasingly unstable supply chain when you could use automation to nearshore or reshore crucial steps in the manufacturing process is an unwise choice that can expose your company to unnecessary financial and reputational risks. Under-automating also puts employees’ quality of life and actual lives on the line. If you’re bogging down employees with repetitive unskilled tasks, you’re missing out on their potential contributions to the organization. In situations where you don’t use the opportunity to automate hazardous tasks, including exposure to harmful substances or physically demanding work that could cause injury, you could be putting their lives at risk and opening the company up to significant liability.
The path forward
What’s the path forward? Finding the “just right” balance between automation and human-powered progress. When you leverage “just right” automation, you’re enabling the broader workforce to have access to jobs that were previously closed off to them and limited to select skilled workers. The ideal setup is flexible and allows for easy adjustments as production needs evolve. This could mean reprogramming robots, reconfiguring work cells, or shifting human workers to different tasks. The best way to identify the systems that could benefit from automation is to lean into data and allow it to drive those decisions. Gather and analyze your data to identify bottlenecks, track performance patterns, and ultimately make informed decisions on when and where to use automation to improve functionality. The goal is sizing automation to “just right,” which should include a hybridization of people, processes, and technology to fit the immediate needs for efficiency and the current state of manufacturing.
It is complicated to find a balance between over-automating and under-automating, but it’s worth the benefits. “Just right” automation allows for vast increases in productivity and efficiency by automating repetitive tasks and allowing human workers to put that time and energy into higher-value activities. Automated systems can reduce human errors and ensure consistent output, so quality and consistency are improved. When robots are leveraged to handle dangerous or physically demanding tasks, human workers are protected from harm and companies are protected from legal liability. Adaptable automation solutions enable manufacturers to respond quickly to changing market demands, thereby greatly improving the flexibility and agility of the manufacturing process. And of course, costs are reduced; automation can lower labor costs, decrease waste, and improve energy efficiency.
When manufacturers can find the right systems to automate and the right places to leverage human resources within their manufacturing lifecycle, everyone from the employees to the company, to the economy and environment, to the consumer “wins.” Goldilocks’ porridge is neither too hot nor too cold; the manufacturing system is neither over-automated nor under-automated. Optimal balance is achieved, and everything is “just right.” It is possible, and it is worth the effort to find it. By implementing "just right" automation, manufacturers can achieve significant improvements in efficiency, productivity, and competitiveness while creating a safer and more engaging work environment for their employees.