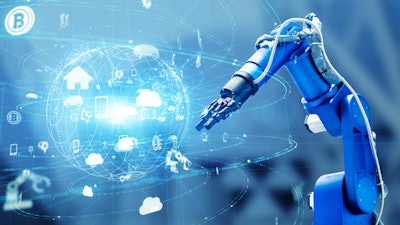
Business continuity refers to maintaining, adjusting or rapidly resuming business functions in the event of a major disruption. Most major organizations have continuity plans in place that cover dealing with critical system/network failure, cyberattacks, hurricanes or price fluctuations in critical materials. Yet how many organizations had a plan in place outlining the instructions and procedures to follow in the case of a “Black Swan” event of global proportions that would unleash volatility, uncertainty, complexity and ambiguity (VUCA) in demand and supply conditions? Very few I imagine.
Since the declaration of the pandemic, many supply chain professionals have had to learn how their organizations were adapting and achieving business continuity by leveraging digital twins.
Here’s how digital twins are helping organizations achieve business continuity during a pandemic.
Phase I: Protect the people and the business
Keep plant operations personnel safe.
The priority at the onset of the pandemic was to keep employees safe. For example, a North American company rapidly incorporated social distancing constraints into their production planning and scheduling digital twins to help keep their manufacturing operations’ personnel safe. While generating optimal manufacturing plans and schedules, the digital twin technology ensures that operations personnel work in a section of the production facility with adequate physical distancing to keep people safe while simultaneously considering complex manufacturing equipment constraints related to using alternating lines/equipment on various days of the week.
Gain insights to financial and operational implications of business scenarios.
The other priority was to protect the financial health of the business. Many organizations mobilized a team responsible for evaluating the financial and operational implications of numerous short to mid-term business scenarios. In one case, a European company had been using their end-to-end supply chain planning optimization digital twin to run and analyze a significant number of scenarios every day immediately at the onset of the pandemic. Their digital twin allows them to easily change time period-specific data assumptions related to supply and demand conditions spanning their global supply chain. Since their digital twin makes use of holistic mathematical optimization methods, they were able to rapidly develop a portfolio of supply chain “game plans” on how to best respond to circumstances as the future unfolds. The big takeaway here is that supply/demand scenarios analysis has skyrocketed in importance in the process manufacturing industries since the beginning of the pandemic.
Phase II: Adjust processes to achieve continuity as supply/demand conditions fluctuate
Keep work-from-home and on-site teams aligned constantly.
Maintaining business continuity and safe reliable supply chain and manufacturing operations became more challenging when some people who usually work at the manufacturing sites were directed to work from home. This included schedulers, material planners, engineers, supply chain planners, shipping coordinators, to name but a few. Even Asian production site used a digital twin to help its supply chain and manufacturing operations teams stay aligned and on the same page throughout the day. The technology allows them to interact with a live web-based view of the latest published schedule, view projected inventory positions, identify problems ahead of time and helps everyone maintain situational awareness about what is happening at the manufacturing facility and working towards a common goal.
Quickly adjust to keep demands, capacity, supply and operations execution in sync.
Another example is of a producer of high-demand materials that leverages a scheduling optimization digital twin to help align demands, capacity, supply and operations execution team members daily. The digital twin allows them to adjust to changing conditions and helps them improve cash flow, ensure on-time shipping performance and flex production output.
Phase III: Prepare for the recovery
Monitor demand for signs of recovery and hopefully rebound.
Since the beginning of the pandemic, most companies are reporting that the accuracy of their demand forecasts are considerably less accurate than before. Forecasting digital twins were never designed to handle the profound and fundamental changes that have occurred in consumer behavior and upstream business demand patterns as a result of the pandemic. In preparing for a recovery, some companies are using digital twins to help them closely monitor changes in demand trends week-over-week as part of their weekly sales and operations execution meetings.
Redesigning supply chain and manufacturing to be more resilient.
The pandemic has exposed the vulnerabilities in today’s global supply chains that were designed for efficiency. There is an opportunity for manufacturers to redesign their businesses to make them more resilient. This will involve analyzing and building redundancies for critical product lines and associated production and supply capabilities, including:
· Reviewing existing suppliers and locations
· Reviewing substitution options in recipes/bill of materials
· Reviewing existing manufacturing locations and the current flexibility of manufacturing resources
This is an area where an end-to-end supply chain optimization digital twin (referenced in Phase I) can be leveraged to explore and analyze various supply chain and manufacturing redesign alternatives to build more resilient businesses.
Digital twins have proven to be tremendously helpful tools to process industry manufacturers in adjusting and achieving business continuity as supply and demand conditions fluctuate.
Implementing or enhancing digital twins will help process manufacturing companies prepare for the VUCA environment that is likely to continue into 2021 and beyond.