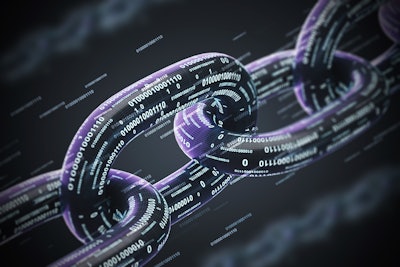
At any given moment, millions of shipments are in transit across the globe—moving through ports, warehouses and distribution centers to meet consumer and business demands. But as supply chains grow more complex, disruptions are becoming more frequent and costly. In fact, a recent study found organizations experience an average annual loss of $184 million due to global supply chain disruptions, with 94% reporting a negative impact on revenue.
Natural disasters are a major contributor to this instability, and their frequency and severity are only expected to grow, potentially crippling logistics operations, delaying shipments and creating cascading effects that harm economic growth.
The need for resilient and adaptable logistics systems has never been greater. The key to success lies in leveraging both emerging technologies—like generative artificial intelligence—and human insight to anticipate challenges and make smarter, faster decisions when disasters or disruption strike.
The resilience gap
Despite technological advancements, many organizations still struggle to view their data holistically and effectively. Organizations often rely on a complex network of partners with varying degrees of technological maturity, with some suppliers operating with advanced digital solutions, while others continue to rely on paper-based processes. This fragmentation creates gaps in data that make it difficult to make informed, real-time decisions, which is needed in times of natural disasters or business disruption.
Furthermore, one of the biggest culprits of this is the use of “dark data”—valuable knowledge and insights that exist within an organization but aren’t captured in formal systems. Experienced workers often rely on intuition to navigate disruptions, making quick decisions based on years of expertise. While effective in the moment, these insights frequently go undocumented, leaving no data trail for future analysis or improvement. Without a system to capture and leverage this institutional knowledge, organizations miss out on critical learnings, making their logistics operations more vulnerable to unexpected disruptions.
When disruption occurs, the reliance on technology that fails to respond in real-time can lead to dangerous, costly delays and poor decision-making. For communities impacted, this means that necessary food, water and gas may not arrive when needed most.
Bridging the data divide
Technology alone can’t serve as the silver bullet to solve for supply chain resilience. Without the right foundational processes, even the most advanced tools will fall short. Organizations must take a step back and focus on bridging the data gap and ensure that critical insights, whether from manual workflows or decentralized operations, are captured and structured effectively.
This process doesn’t always require cutting-edge innovations; in many cases, it’s about getting the fundamentals of data capture and process interdependency right. A key factor for success is embedding exception management workflows into daily operational applications, so organizations can capture “dark data” and prevent issues from being resolved outside the system. By taking this approach, organizations can bring structure to fragmented supply chains by digitizing manual inputs and transforming them into actionable insights while streamlining the overall process.
Once organizations have built this foundation, they can take the next step and leverage tools such as AI to optimize decision-making. Capturing how exceptions are handled in a digitized format allows for the creation of synthetic datasets, particularly when data is scarce or sensitive, and allows for faster AI training, testing and validation. The key to achieving this is business process reengineering—rethinking how data is collected, shared, and utilized across the supply chain. With the right processes in place, technology becomes an asset rather than a standalone solution, helping companies turn real-time insights into resilient, data-driven operations.
AI and automation
AI-powered optimization is transforming many industries, enabling them to move from reactive responses to proactive strategies. The same is true for supply chain management, where companies are using AI in the planning processes to analyze real-time and historical data to predict potential disruptions before they happen, along with their potential impact. With these insights, organizations can build contingency plans that go beyond surface-level fixes, ensuring they have an executable strategy in place no matter what happens.
What sets AI-powered optimization apart is its ability to account for the complex interdependencies quickly within supply chains. A disruption doesn’t just affect a single shipment—it has a ripple effect across production schedules, inventory levels, transportation networks and customer commitments. AI doesn’t just identify risks; it helps organizations understand the cascading impact of these disruptions, allowing for smarter, faster decision-making.
Emerging technologies
Beyond AI, the next wave of resilience in supply chains will be driven by emerging technologies that help structure and optimize data in ways we haven't seen before. Computer vision is set to advance how teams manage physical operations like spacing, capacity and potential constraints. For instance, a truck may be planned to carry a specific volume, but real-world factors—like an unnoticed dent affecting available space—can disrupt that plan. By feeding real-time, visual data into AI systems, companies can reoptimize on the fly, adjusting plans to reflect actual conditions and improving overall accuracy. This level of visibility will take predictive analytics to the next level, driving smarter automation and more efficient operations.
Additionally, speech recognition—technologies that convert speech to text and vice versa—are also transforming learning processes and knowledge management. These systems can take insights from workers on the ground, feed them into smaller language models and then compare that data against larger datasets to refine decision-making over time. In practice, this helps to turn everyday observations into structured, actionable insights that improve operations.
Though still emerging, quantum computing holds significant potential for revolutionizing supply chain resilience. Its ability to solve complex optimization problems far faster than traditional systems could lead to highly efficient route planning, better demand forecasting and stronger disruption management. While still in its early stages, companies that prepare for quantum’s future capabilities stand to gain a competitive edge.
The road ahead
The future of supply chain resilience lies in embracing technology that provides greater visibility, predictive capabilities, and real-time responses to disruptions. By integrating AI and emerging technologies, logistics companies can create a more agile supply chain that can quickly adapt to challenges, including the ever-growing threat of natural disasters.
However, the path to resilient supply chains isn’t just about chasing the latest technology—it's about laying the groundwork for smarter, more adaptive operations. The future belongs to companies that recognize resilience as an ongoing process, combining human insight with technological innovation to navigate uncertainty and keep goods moving, no matter what challenges arise.
As natural disasters and daily disruption continue to pose significant threats to global supply chains, it’s essential that logistics organizations prepare for the unexpected. With the right combination of technology and human insight, companies can weather the storm and maintain operations in the face of even the most severe disruptions.