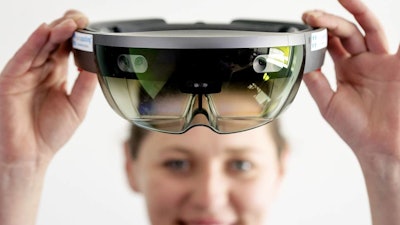
Until early this year, the business migration to Industry 4.0 had seen a variety of connected technologies undergoing tests and being implemented in manufacturing and heavy machinery industries. This included high-quality sensors, robust networks, powerful computing systems, artificial intelligence and immersive technologies such as augmented reality (AR) and virtual reality (VR). Then the Coronavirus disease (COVID-19) hit.
The disruptions that flowed from the frightening surge of COVID-19 cannot be overstated. Offices, stores, restaurants, hotels, ships, schools and factories were either shuttered or left to limp along with sharply reduced staffs and greatly enhanced housekeeping. Beyond that, it revealed the limited resilience of most heavy machinery and related industrial businesses that depended on manual processes.
But, certain essential services like utilities, continued operating at pre-pandemic levels, while other industrial facilities began to cautiously reopen, trying to balance their operating needs with the safety of their personnel. As with every setback, people continued to persevere, plan and innovate.
Before COVID-19 hit, the impact of Industry 4.0 could be felt in a number of ways. For example, technologies like industrial additive manufacturing, valued at over $10 billion, had disrupted supply chains and challenged established ‘subtractive’ processes like machining metal blocks. In addition, there were massive changes in data processing involving state-of-the-art sensors, artificial intelligence, high-performance computing and advanced machine learning. As a result, unmanned systems began understanding complex commands and performing complicated tasks with minimal human intervention.
But now, in the throes of the pandemic, organizations of all sizes are realizing that to be competitive, digital technologies need to be implemented across all business and operational functions. Conversations have moved from “how do we create a smart factory?” to “how do we keep production going during this time?” The answers to those questions have only accelerated the adoption of new technologies and digitization of processes.
Since employees are now working from home, digital collaboration tools have been widely adopted. As a result, a worker’s digital and physical worlds now converge in many areas. They range from cyber-physical systems and digital twins that predict real-time collisions along a machining tool path to real-time repair and maintenance using AR apps for smartphones and glasses. That convergence becomes even more evident with newer AR apps that allow the user to interact with a real-world environment – adding virtual objects that blend-in, providing the user with realistic visual feedback and a more immersive experience.
This Wall Street Journal story talked about an Intel semiconductor plant in Arizona that had hit a stumbling block. It needed to recalibrate its machinery along with installing new equipment to meet surging demand. But, the engineer who had specialized in that sort of work was stuck in Germany because of transatlantic flight restrictions brought about by the Coronavirus. The solution? By repurposing a set of AR goggles, the Arizona workers were able to show the stranded engineer the issue they were facing, enabling him to walk them through the repairs.
The article also noted that the use of AR glasses by U.S. car dealerships had tripled during the pandemic, as technicians sought virtual help from experts hundreds of miles away.
As these examples indicate, organizations are moving from hypothetical AR scenarios to pragmatic use cases resulting in better efficiency, higher productivity and improved safety. The technology is poised to optimize the value chain for organizations of all sizes and across different industries, including the aerospace, automobile, manufacturing, oil and gas sectors where it is being used for practical applications like remote guidance and expert assistance.
Manufacturers today face a combination of turbulent global markets and shifting employee demographics. Automation and advanced machine learning, although promising, have not yet reduced the burdens on assemblers, operators or technicians. Although operation centers, over time, became geographically dispersed to cater to regional demands, the availability of skilled workers never kept up, leading to a disparity in workforce knowledge and expertise. In response, over the last decade, many companies have assigned experts from their different facilities networks to support local customers.
But, restrictions resulting from the COVID-19 pandemic disrupted this arrangement. The “New Normal” has translated into a combination of severe travel restrictions, lack of hands-on training, fewer on-site staff and disrupted supply chains. It has pushed companies into rethinking ways of accelerating the optimization of their processes and of driving productivity improvements to enhance business performance.
In response, some organizations have adopted AR technologies to maintain business continuity while mitigating any impacts on health. Remote assistance using AR enables experts to connect with on-site users in real-time to offer guidance involving inspection, repair, or maintenance – all within the context of real applications. The opportunity to digitally augment real-world images from a remote location greatly enhances the clarity of communication and improves collaboration. The same technology is even being used for after-sales training with users and operators.
Consider the case of maintenance, repair and overhaul (MRO). MRO activities are not only among the most critical areas of engineering for economic growth and industrial operations; they are also ideal candidates for AR in both developed and developing economies. The global market for AR in MRO was valued at $403.3 million in 2018 and is expected to reach $3.3 billion by 2024, growing at a CAGR of 42.1% during the forecast period 2018-2024.
At the same time, however, using AR in a safe, productive and consistent manner in a factory setting requires changing plant operating procedures. For example, distinguishing operations that need to be done on-site from those that can be done remotely; providing protective equipment to frontline workers; revisiting workplace safety practices; managing production schedules with staggered shifts to meet social distancing requirements; leveraging automation and remote monitoring technologies; and implementing contactless systems such as AR to minimize touch and provide workforce training.
There will come a time when the pandemic will have faded into history. But, legacies of the response to coronavirus, including AR, will almost certainly continue, expand, and accelerate the transformation now underway toward a more resilient, more adaptable, more digital industrial future.