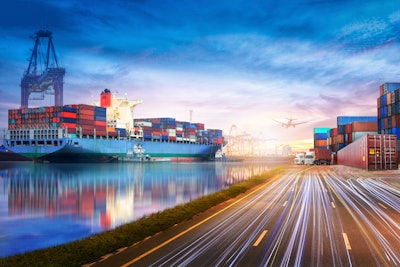
With consumer goods companies gearing up for the Christmas shopping season, there is a flurry of activity taking place behind the scenes that most consumers are unlikely to be aware of. The pressures and strains placed on global supply chains and transport services have only increased with the recent disruptions faced in the Red Sea, congestion in ports and the increased cost of container rates. These issues highlight the vulnerability of supply chains and the knock-on impact these delays have on getting goods to shelves in time for the biggest shopping season of the year.
With these challenges weighing heavily on the minds of business leaders, it is vitally important to ensure that organizations look to minimize - and ideally eliminate – disruptions, by ensuring that they have accurate inventory levels to ship, ensuring smooth global trade.
Building Supply Chain Resiliency
With the global supply chain currently navigating a maze of challenges that have only continued to escalate since the beginning of the year, there is an increasing need for businesses to build more resiliency into their supply chains. By being able to anticipate and react to changes in the supply chain for any potential disruptions, businesses will be able to gain an advantage in determining the best possible actions to protect their supply chains from bottlenecks.
Capgemini’s ‘Fast Forward’ report found that more than 57% of organizations are increasing their investments to enhance the resiliency of their supply chains, and that, for many organizations (62%), increasing their supply chain resiliency is a key priority.
One of the key aspects in building resilient supply chains is visibility. High quality supply chains thrive on the deep understanding of the flow of raw materials and goods. Despite this core tenet of operations, only 6% of logistics companies claim full visibility of their operations, warehousing being the hardest one to collect insights from.
Through visibility, businesses can detect issues early and allow organizations to rapidly identify issues that could cause delays at various stages of the supply chain. This means that companies can take proactive measures to mitigate against them.
The Role of Accurate Operational Visibility and Management
With built-in resiliency and visibility, businesses can tackle critical issues. However, at every stage of the process, it is important that businesses have visibility of their inventory throughout the supply chain. In this complex environment, maintaining accurate inventory is not just a logistical necessity, but also a strategic imperative. Here’s why:
- Minimizing Delays and Downtime: Accurate inventory data ensures that businesses can respond promptly to supply chain disruptions. Knowing the exact location and status of goods helps in rerouting shipments efficiently, thereby minimizing delays and avoiding costly downtimes.
- Optimizing Resources: Companies can avoid the pitfalls of overstocking or understocking, which can either tie up valuable capital or lead to stockouts and missed sales opportunities. This balance is particularly crucial when dealing with fluctuating shipping rates and unpredictable supply chain interruptions.
- Enhancing Customer Satisfaction: Reliable inventory levels ensure that customer orders are fulfilled promptly, maintaining trust and satisfaction. In a competitive market, the ability to meet delivery commitments can be a significant differentiator.
- Reducing Costs: Accurate inventory helps in forecasting demand more precisely, which in turn aids in negotiating better shipping rates and terms. It also reduces the need for emergency shipments, which can be significantly more expensive.
- Supporting Strategic Planning: With precise data, companies can plan more effectively for future demands and potential disruptions. This strategic foresight is invaluable in navigating scenarios where supply chain conditions are volatile and unpredictable.
Preparing for the Future: Scenarios, Strategies and Digital Twins
There are still many challenges that could cause disruptions ahead of the busiest shopping season on the calendar, with many issues - both geopolitical and planning related - that could cause bottlenecks in the supply of goods from factory to the store and to the hands of consumers.
In terms of how to mitigate the risks, there are ways that using intelligent technology can help businesses overcome some of the challenges.
- Worst Case: Should disruptions continue on key shipping routes and the peak-season demand reaching good levels, there could be effects felt on how and when goods will be delivered to consumers. In this scenario, accurate inventory tracking is vital to manage extended lead times and avoid crippling shortages. Using powerful AI features will allow businesses to analyze data from previous shipping routes and the efficiency in which goods arrive in their locations to better determine the optimum routes to get the goods into the hands of consumers.
- Best Case: In the best-case scenario, there are no delays caused by the availability of containers or geopolitical tensions. Combining these ideal conditions, it is likely that cargo rates could drop as supply outpaces demand. Here accurate inventory management would enable businesses to capitalize on lower shipping costs and rebuild stock levels efficiently.
- The middle ground: What could happen in the most likely scenario is that demand decreases from previous years due to the prolonged recovery from sharp interest rate rises. This could still have an impact on the rates of containers, which could lead to organizations to look at their commitments. However, an accurate and real-time view of their inventory will help organizations navigate fluctuations and ensure that they are neither overcommitting nor under-prepared.
In the face of global supply chain challenges, the importance of end-to-end visibility, as well as accurate inventory management cannot be overstated. It serves as the backbone for minimizing delays, optimizing resources, enhancing customer satisfaction, reducing costs, and supporting strategic planning. As the industry navigates through the uncertainties of 2024 and prepares for 2025, businesses that priorities precise inventory tracking will be better equipped to mitigate disruptions and sustain their operations in a volatile market.