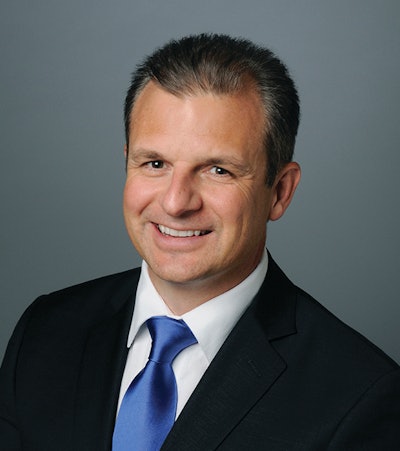
Real-Time Data, On-Target Decisions
Even if your fleet consists of only a handful of trucks, chances are you make hundreds of decisions, including dozens on a moment’s notice.
But how good are those decisions? Research reveals that even the most unassuming of us are overconfident in our decision-making abilities, partly because our brains are flawed instruments and partly because we often let our emotions get the best of us. What’s more, we seek out information that supports our decisions and ignore that which doesn’t.
So how can you make better, more well-informed decisions about your fleet? One way is to base your decisions on factual, unbiased data provided by on-board computers (OBCs). Most private fleets have relied on such devices for several decades—at first to track their vehicles and message their drivers, and later to monitor hours of service (HOS) compliance and increase driver productivity.
Now, in an effort to accelerate and improve return on their entire supply chain, today’s leading fleets are turning to next-generation fleet management systems. The result? Less guessing, more accuracy. Less waste, more efficiency. Less cost, more profit.
Data-Driven Decisions Propel Exceptional Performance
According to recent Gartner research, three obstacles hinder a company’s ability to make well-informed decisions about its supply chains:
- Inability to accurately forecast.
- Lack of integrated processes.
- Fragmented data.
But thanks to advances in fleet analytics, many of today’s leading fleets are more closely aligning their people, processes and technology to make better decisions about—and derive more value from—their supply chains. Fleet management systems are at the core of this movement.
Many OBCs act a vehicle’s smart hub or mobile hotspot for exchanging the following two types of actionable data that companies can use to make confident decisions about their entire supply chain:
- Data drivers need. All critical information drivers need—such as turn-by-turn directions, delivery instructions, last-minute customer requests, road closures, and weather and traffic alerts—is sent to the OBC, and either relayed audibly or displayed on the system’s 7-inch color touchscreen. Drivers also receive information about their own behaviors, such as speeding or hard braking.
- Data fleet managers need. The OBC automatically collects and transmits data, such as mileage, speed, miles per gallon (MPG), revolutions per minute (RPM), idle time and sudden decelerations. It also logs and provides managers with the data that drivers enter into the system themselves via the touchscreen, such as hours of service, unexpected delays and delivery details.
The smart hub concept is growing in popularity with fleet managers for several reasons:
- Its software-as-a-service (SaaS) model gives fleets of all sizes access to a single, easy-to-use application. No more information technology (IT) overhead, expensive hardware or lengthy implementations.
- It easily integrates with other systems, such as time and attendance systems, tire-pressure and temperature monitoring systems, routing and delivering systems, and warehouse and third-party logistics systems.
- It collects real-time data vs. “already out of date” near-time data, integrates that data and makes it available anywhere, anytime via colorful dashboards and easy-to-generate reports.
What makes these reasons so compelling? According to an annual global survey of supply chain progress, companies with strong supply chain visibility and analytics capabilities are nearly twice as likely as others to reach the top 20 percent in business growth.
Fleet Management Technology: The Key to Smarter, Faster Decisions
Fleet management technology collects real-time data about every aspect of a fleet’s operations—from routing and dispatch to customer delivery, from driver payroll to fuel taxes, from inventory management to vehicle maintenance—and seamlessly integrates that data with data from other systems so that fleet managers can make smarter, faster decisions about every aspect of operations.
Take decisions about drivers, for instance. Drivers are the lifeblood of every private fleet. The best drivers operate responsibly: They are drug and alcohol free, drive the speed limit, and keep a safe distance from other vehicles. They also make their pickups and deliveries on time, and treat the goods they transport with care and the customers they serve with respect.
What’s more, these drivers typically outperform other drivers by significant margins.
In fact, data shows that a fleet’s most efficient drivers get about 30 percent better fuel economy than the least efficient drivers. They also have fewer accidents and duty status violations.
Most fleet managers know in their guts whom these drivers are. They may also suspect whom the troublemakers are, yet without the right evidence to prove this disparity, many poor performers remain on the payroll. Keeping bad drivers poses a risk for every company, but especially for private fleets, where one serious accident can have a multi-million dollar impact on a company’s bottom line.
Rather than putting their companies in jeopardy, fleet managers can use the comprehensive driver data to take corrective active action against their worst drivers—and reward their best. For example, some fleets create performance-based incentives, such as monthly or quarterly bonuses for drivers with the least idle time or the most on-time deliveries.
By making it so easy to administer such systems, fleet management systems increase driver satisfaction by automating routine tasks, such as recording mileage and hours of service, and completing pre- and post-trip inspection reports. By automating these tasks, driver admin time is reduced by up to 15 minutes per day per driver, while also increasing safety and compliance.
Not only are your drivers important assets, but so are the vehicles they drive. By helping you make smarter, faster decisions about when, where and how to use them, fleet management technology helps reduce vehicle-related costs and increase profits.
And with a full load of 24/7 real-time data about each vehicle, including speed, miles traveled, MPG, RPM, hard braking and more, you have all the information you need to make well-informed decisions about maintenance and vehicle replacement.
Fleet management technology also gives you unprecedented visibility into vehicle and tractor locations, both real time and historical. Global positioning system (GPS) tracking and mapping automatically track drivers and vehicles so you can optimize delivery routes and reduce out-of-route miles, all while keeping close watch on your inventory.
What’s more, up-to-the-minute vehicle location and speed data enable you to manage last-minute changes, including unexpected road closures or dock delays. This same information also enables you to say yes to last-minute customer pickup and delivery requests, or company-ordered backhauls. As a result, customer satisfaction improves. So does capacity and vehicle utilization.
Driving Decisions the Data Way
Reaching the right decision at the right time can make all the difference to your supply chain. Make every decision the right decision by choosing a fleet management system designed to meet your company’s unique needs.
Tom Flies is the chief operating officer of Cadec Global, Inc.