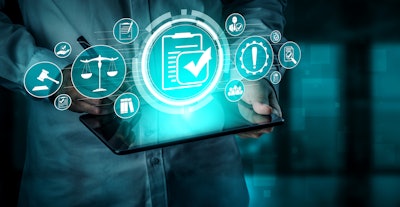
The stock market’s recent downturn—and the decline in manufacturing activity over the preceding months—signal less-than-ideal times ahead for our industry. Of course, market turmoil isn’t new to manufacturers, with the past few years alone having shown just how volatile things can be. Fortunately—due to the ways many businesses pivoted to contend with the COVID pandemic—global supply chains are on solid footing. However, a firm foundation should not dismiss the need for continued innovation: supply chains are only getting more complex and financial concerns are again bubbling to the surface.
Though it’s impossible to say for sure what the coming months and years will hold, achieving significant, sustainable success will undoubtedly hinge on a business having the type of operational flexibility that is born out of meticulous, data-based planning.
Not Just Numbers
The industry’s move toward connected, data-driven operations has been underway for some time, and its impacts on business outcomes have been significant. Manufacturers have embraced a data-led approach to supply chain management to better anticipate demand, materials shortages, and downtime with resource planning and forecasting software.
The results have been less waste, better products, and improved bottom lines. However, implementation isn’t a “one-and-done” task. A truly data-led operation rooted in continuous improvement and maintaining these systems is an ongoing endeavor. Now that the initial investments in digital transformation have been made, leaders must turn their attention to a major byproduct of their investments: data.
To ensure the level of agility needed in today’s market, manufacturers must commit to continuously improving their methods of collecting, storing, interpreting and using their records. That’s where data management planning comes in.
Data management plans are similar to project roadmaps leaders may have created to guide their digital transformation journeys or AI adoption initiatives. They outline key processes around ongoing data program maintenance, integration, access, and more to ensure that businesses derive as much value as possible from their investments in connected monitoring.
To begin developing your management strategy, consider:
Collection processes. Most manufacturers are well-versed in the importance of robust and accurate data, but many don’t realize that their current practices are lacking in efficiency and accuracy. In fact, despite the growing popularity of connected monitoring systems, only 2% of North American manufacturers say they collect all of their data digitally. Even among manufacturers who say they have “completed” their digital transformations, the number still collecting at least some data through manual reporting is surprisingly high (61%).
To kick off data management upgrades, manufacturers should consider investing in an ecosystem that uses industrial Internet of Things (IIoT) sensors to track changes and performance in real-time. This helps minimize the likelihood of human error in datasets, highlight trends in progress, and streamline validation and reconciliation.
Storage needs. Connecting a facility and engaging in real-time monitoring is great, but all that data needs somewhere to go. Leaders must also invest time in building robust storage infrastructure that can grow alongside operational datasets. With all sources necessary to get a full picture of operations, those storage demands add up quickly.
There are a few options available to manufacturers as they seek to build adequate, scalable storage architecture: cloud-based (which can offer enhanced flexibility), on-premises (which can reduce latency but requires bigger upfront investments), and hybrid. As with many aspects of digital transformation, there is no single “right” choice. Each manufacturer will need to review the options available to them and decide which approach makes the most sense for their current operations and future goals.
Potential for integration. Leaders also need to consider how all their enterprise data needs to intersect. As digital transformation rippled through enterprises, departments and business areas implemented their own systems at different points in time. In order to make effective predictions, analytics tools must know what’s happening both on and off the factory floor.
To get the level of insight needed in today’s market, though, manufacturers must find a way to unite those disparate sources and datasets to get a clear picture of the pressures they may face. It’s also important to consider how you will handle any existing records that need to be added to the system since historical data can form a useful baseline for future performance assessments.
Accessibility and security. Data is only valuable if it's available to those who need it, so it's crucial to plan how employees will interact with and access relevant records. Connected platforms may have built-in dashboards with customizable access controls to ensure everyone has what they need to engage with operational insights in ways that work for them.
Of course, denying access to bad actors is just as important. Storing data can come with risks—especially related to customers’ financial details, proprietary documents, and other sensitive information—and connecting equipment can open enterprises to physical safety concerns as well. With this in mind, manufacturers should keep the importance of consistent data security protocols in mind from the start and seek out vendors whose systems adhere to existing industry standards.
End-to-End Planning for End-to-End Insight
With just a few years between COVID’s disruptions and this month’s economic strife, manufacturing operations are about to be put through another test of resilience. No one knows exactly how the disruptions will shape up, but leaders in the space can be certain of at least one thing: agility will be the make-or-break feature of modern production operations.
Though the specifics of the journey will vary based on a business’s needs, the principles outlined above provide a solid framework for the task ahead. Success will hinge on each manufacturer’s ability to develop the flexibility and predictive acumen needed to guide effective, timely course corrections.