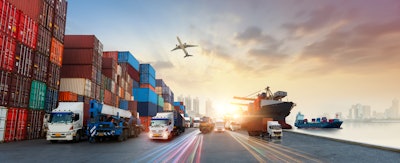
The supply chain has taken a real beating since the COVID pandemic broke out in early 2020, and, unfortunately, every time it seems about to recover back to something resembling “normal,” another event puts it out of whack once again. And while I wish I could say that the outlook for the next six to 12 months is a reversion to the mean, the “new normal” for the supply chain is constant disruption with ongoing slow improvement between new crises.
Here's a good illustration of what I’m talking about: Right now, we’re in the midst of a game of supply chain whack-a-mole. The good news is that West Coast ports, which were famously clogged with dozens of container ships waiting weeks to dock and unload their cargo, have largely taken care of the backlog and are once again running smoothly. The bad news? So many companies altered their supply chains through East Coast ports when the West Coast was all jammed up that now the East Coast ports are becoming constrained.
What’s more, there’s another potential problem on the horizon. West Coast port labor has been working without a contract since May 2022, so the possibility of a disruptive strike is looming if negotiations this year take a bad turn. Shutting down West Coast ports, even for a short period of time, would have a disruptive ripple effect throughout a supply chain that’s already under significant stress.
Additionally, China’s Zero Covid policy was causing supply chain disruptions whenever cities with large manufacturing facilities would suddenly go into lockdown, which shut down production and delivery of critical components and finished goods. However, when China abruptly reversed this policy in December 2022, an apparently severe wave of COVID infections broke out in a variety of locations throughout the country. The impact of this COVID wave is hard to predict, but further disruption to the supply chain seems inevitable.
If that’s not enough, there are further wrenches in the supply chain works. Ukraine has long been a major supplier of grain, fertilizer and petroleum, as well as a key producer of raw materials such as aluminum, nickel and potash. The Russian invasion and ongoing war have made production and export of these materials extremely difficult, if not impossible.
While inflation has come down somewhat in recent months, it remains three to four times higher than it has been in decades. It continues to put pressure on all stakeholders in the supply chain.
Strategies for dealing with the volatile “new normal”
In a world where the new normal is constant disruption, manufacturers and distributors need to prepare so they can rapidly identify and mitigate risks.
The first step is to digitize operations to the highest degree possible. Information in paper documents is inaccessible to technologies like AI and analytics, which have the ability to provide powerful predictive insights that enable people to make accurate, rapid decisions in the face of constant change.
Additionally, it’s critical to create strong, transparent relationships with suppliers and buyers to gain deeper visibility into what’s happening further down the chain so everyone can take appropriate measures. It’s hard to share bad news, but it’s far better to share it early with customers and partners so they can be prepared. Doing so will strengthen trust and enable everyone to adjust their operations to mitigate their risks.
Another strategy is to take measures to shorten the supply chain so it’s less vulnerable to disruption. After all, the fewer links there are in the chain, the less likely one of them will break. Many companies have already begun this process. According to Deloitte’s “Future of Freight” report, companies are expected to have reshored 350,000 jobs in 2022, which is 25% more than the previous year. Ultimately, this will reduce the share of shipments from APAC as much as 20% over the next three years.
Finally, manufacturing and distribution organizations need a strong ERP platform to bring all of these efforts together. ERP serves as the technological foundation for digital transformation, providing a single source of the truth for supply chain management. It’s where all information about the supply chain resides and — if it’s a well-designed, flexible platform — will have built-in analytics capabilities to provide timely supply chain insights, along with the ability to connect it to AI and machine learning to provide additional predictive power.
We live in interesting times, no doubt, and the supply chain is volatile and unpredictable. But with the right preparation — digitalization, good communication with suppliers and customers, shortening the supply chain and deploying a solid ERP foundation — manufacturers and distributors will be able to successfully weather whatever the world throws at them.