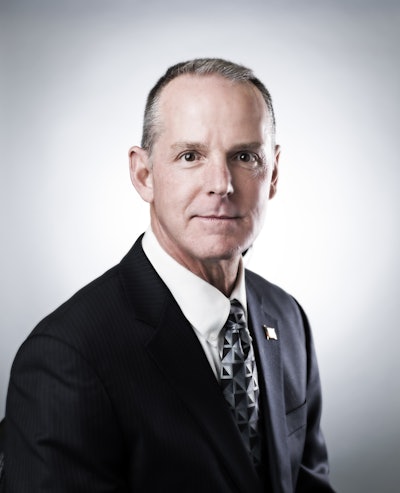
The growth of online retailing driven by the shift from brick-and-mortar stores to online shopping is resulting in the dramatic growth of distribution centers across the globe. At these sprawling facilities, safeguarding employees and reducing shrink is proving very challenging.
Today’s distribution centers face a number of threats to the security of employees and assets—theft, vandalism, employee violence and more. In addition to ensuring that these distribution centers are meeting accuracy and delivery demands, security directors are tasked with making sure assets, employees and inventory are kept safe and secure at all times.
More Effective Loss Prevention
In today’s distribution centers, a variety of merchandise passes through on a daily basis and numerous employees work varying shifts, which can make it difficult for security professionals to continuously monitor merchandise.
For many retailers, archway metal detectors and hand wands are the standard technologies currently being implemented; however, each only provides an audible beep whenever a metallic item is detected. This presents a challenge to loss prevention personnel to identify the cause of the audible alarm. In the case of non-metal objects, the items go completely undetected with these traditional screening methods.
Distribution centers handle a variety of merchandise that is manufactured from a wide variety of materials—often with little or no metal. There is a significant need in the loss prevention industry for technologies that can detect a broader number of materials, such as metals, plastics, powders, ceramics, gemstones and even clothing.
Another challenge for these centers is the hundreds, and even thousands, of employees who enter and exit on a frequent basis, including full-time, part-time, seasonal and transitional workers. To achieve a return on investment (ROI), retailers should look for a security solution that offers a streamlined screening process while delivering a high level of protection for both employees and merchandise.
One such technology solution utilizes thermo-conductive infrared (IR) technology that utilizes heat transfer to provide high-resolution images without using harmful ionizing radiation. The images created show thermal imprints of concealed objects under clothing. This allows loss prevention professionals to visually identify specific objects hidden under an employee’s clothing—whether it’s contraband or merchandise—and respond in an appropriate manner.
Addressing Screening Privacy and Health Issues
Traditional screening technologies, such as metal detectors and hand wands, can also create privacy issues. For example, if an employee sets off an alarm and is detained for a period of time, then discloses that he or she has a metal piercing, that experience can cause embarrassment and distrust for employees and employers, and may even result in legal action. There is a fine line between deterring merchandise theft and ensuring that employees feel respected during the process.
More invasive screening—such as the backscatter X-ray and millimeter wave devices used in airports—are also associated with privacy and health-related issues.
Reducing Screening Time
Another challenge that distribution centers face is the time it takes to screen employees after their shift is completed, when hundreds of employees are exiting and hundreds more are entering the facility. The issue emerges when employees have to wait for extended periods of time before being able to clock in or out.
In late 2014, the Supreme Court rejected a claim by Amazon employees seeking wages for time they spent being screened for stolen merchandise. They claimed that they should be paid for the amount of time it took to be screened, since shift work created bottlenecks of incoming and exiting employees. Despite the ruling, employers have a vested interest in keeping bottlenecks to a minimum in order to avoid frustrating their employees.
New IR imaging technology helps streamline the screening process by offering operators instantaneous imaging results, which allows security officials to quickly decide on whether a threat exists or an employee is attempting to steal merchandise. Clearer images speed the screening process significantly by allowing operators to see objects clearly and distinctly, and giving them time to sound an alarm or detain the person being screened.
A clear image also helps keep security professionals from getting into a situation in which they are falsely accusing employees, which in turn, creates a negative work environment. The key is that these images provide true probable cause.
An Answer to New Threats
The large variety of employee demographics in today’s distribution centers can also result in challenges. Often seen as a taboo topic, workplace violence can become a very real threat when so many different people share and work in the same space, many making minimum wage or acting as transitional workers. Many companies today do not screen employees as they enter the building, potentially incurring large liability if there was a preventable incident of workplace violence resulting in death or serious injury.
The threat of workplace violence in distribution centers recently became a more high-profile topic, with news outlets reporting an influx of violence in the workplace. However, security officials tend to focus primarily on the loss prevention side, which leaves this topic of workplace violence in the dark. Today, workplace violence is becoming more prevalent as the security industry and the nation see more and more incidents on a daily basis.
The bottom line is that today’s distribution center executives and those of the future need to look at ways they can be more proactive in protecting the lives and well-being of their employees from workplace violence. Investing in technology that can be utilized both at the entrance and exit points of a facility can not only protect employees, but also better prevent merchandise from potentially walking out the door.
The Future Is Bright
Distribution centers have some of the best technology available to them to help deter and detect loss, protect employees from potential violent threats, and prevent wrongful accusations. Investing in this technology not only helps businesses significantly reduce liability exposure, but also enables organizations to maximize the return on their investment.