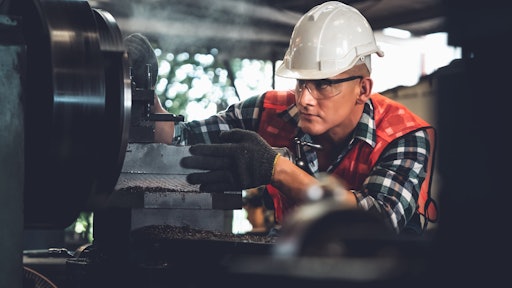
There is no shortage of activity happening within U.S. manufacturing in 2024, as the sector stabilizes and shows signs that it is on the cusp of recovery after a few rocky years.
At the same time, it would be foolish to ignore the multi-layered talent and skills gap that still presents the capabilities to be a thorn in US manufacturing’s side. Yes, the landscape is changing fast, but there are two numbers that we cannot ignore amid a positive resurgence.
One, there remains a projected 2+ million unfulfilled jobs by 2030, according to the Manufacturing Institute. Two, manufacturers are struggling to full “middle-skill” jobs that require some level of technical training or applied skills, such as maintenance technicians, welders, and computer numerical control (CNC) machinists.
A potential problem lingers. A new generation of workers are needed to fill the talent pipeline, but many need additional skills training or upskilling opportunities in a new world of manufacturing. And, while manufacturing is emerging as a well-paid, resilient profession, historically, there has been a level of domain expertise that has kept people from maximizing new opportunities.
Here’s the good news. Through combination of technological transformation and grass-roots education, manufacturers and the industry at large can attract new and current generations of the workforce, close lingering talent gaps, and reposition itself in the minds of people around the nation.
Build It and They Will Come – Manufacturing’s New Frontier
One trend continuing in 2024 is the U.S.’s funding efforts to support the revival of manufacturing – and to promote resilience through reshoring or nearshoring. This includes the manufacturing construction boom as many of the industry’s major players look to establish new factories and modernize operations.
This is critical and digital transformation is a key driver. In fact, a recent Deloitte study indicated that more than 80 percent of surveyed manufacturing executives believe that smart factory solutions will be the primary drivers of competitiveness in the next five years. Why? Because smart factory solutions are best positioned to improve efficiency, agility, and resilience during turbulence or potential economic uncertainty. We’re already seeing huge investments from manufacturers in making factories intelligent and connected – from installing automated machines that speed up and increase the repeatability of line changeover, to deploying dynamic machine monitoring and machine-to-machine process control for data-driven agility.
Bringing this back to talent, the Deloitte report took it one step further. It states that improving talent attraction and retention is tied to leveraging new digital tools. The previously mentioned funding doesn’t hurt either. The average hourly earnings of employees in manufacturing continues to rise, with manufacturing noted as one of the top industries to explore a pay raise in 2024. This looks like a very attractive proposition for an emerging wave of talent. A well-funded profession with lots of national investment. A digitally powered workplace with tools that support worker preferences. A more flexible and higher paying job that continues to improve its employee benefits.
Filling Talent Gaps by Broadening the Talent Pool – and Making Manufacturing Accessible
During any time when the workforce shifts, doors can open for employees needing or looking for a change. A good example is the current technology workforce, which is currently undergoing a shift following the highs and lows of the past decade or so. This can result in a growing candidate or talent pool that is educated, experienced, and motivated.
Can the manufacturing industry benefit from this change? Yes – and in addition to competitive salaries, benefits, and workplace structures, there are two additional steps manufacturers can take to attract new workers: lower the barrier to entry with simpler-to-use technology and provide adequate training and reskilling programs to tighten learning curves.
Both of these ideas have been talked about since the dawn of industry 4.0. However, in the past few years, solution providers have really hit their stride when it comes to ease of use. As a result, manufacturers can then change how they skill. Spurred by the infusion of intelligent, automated, and connected tools, manufacturers can supplement or augment certain parts of the manufacturing process. And they can make teaching a lot simpler.
For example, many advanced screen printers now come with unit cleaning for each printing cycle and sensor networks that predict maintenance requirements. Rather than needing to know how to break down a machine and prep it for changeover or put machines on repair cycles that are either too early or too late, manufacturing line workers can focus on more strategic tasks like material analysis or quality control – leading to greater efficiency and savings. And it gives analytical minds a chance to drive business value and solve for customer needs, as opposed to reading manuals on machine repair.
A New Generation of Workers are Arriving – Make Sure They’re Ready When They Get Here
A digitally powered manufacturing plant is being built. The workforce is shifting, and the workplace is modernizing. Manufacturing is a great profession again. That is wonderful news, and here comes an eager, hungry, youthful generation of workers graduating from education systems around the country. Are they ready – and positioned to be successful? Thanks to dedicated manufacturing programs being established at the college level that involve BOTH theoretical and practical learning, they might soon be.
Here's an example. Lorain Country Community College offers an Associate of Applied Science in Mechatronics Technology – Micro Electromechanical Systems (MEMS). This program – which is a build on of an MES certificate program – gives students a bit of theoretical coursework and hands on experience working at the operator level. This includes hands on time with materials, equipment, protocols, and processes related to the microelectronics industry. A well-designed manufacturing processes course equipped with on the ground labs, plant visits, and manufacturing job fairs can be effective in changing student's perception of manufacturing.
Manufacturing will also benefit from industry-wide initiatives and endeavors, such as the STEM Careers Coalition and work from other associations that continue to move the industry forward. This includes mentor networks. In talking with people across the industry, one of the most underserved areas within manufacturing is mentorship. More than 75 percent of workers think mentors are important, and yet less than 40% have them. Furthermore, 97% of individuals with a mentor find the experience to be valuable. So, for those in the industry wanting to leave a positive impact on the next generation, don’t shy away from mentorship as a driver of added value.
Gearing Up for the Future
The next generation of manufacturing workers have a lot to look forward to as the industry retakes its place as an impactful, established, and proud economic driver in the eyes of the nation.
Watch this space – and, if so inclined, join it. U.S. manufacturing is here to stay.